Rear Differential Carrier (For 2Ad-Fhv) Inspection
INSPECT RUNOUT OF DIFFERENTIAL RING GEAR
INSPECT DIFFERENTIAL RING GEAR BACKLASH
INSPECT TOOTH CONTACT BETWEEN RING GEAR AND DRIVE PINION
INSPECT DIFFERENTIAL SIDE GEAR BACKLASH
INSPECT DIFFERENTIAL SIDE GEAR BACKLASH
INSPECT RUNOUT OF DIFFERENTIAL DRIVE PINION
INSPECT DIFFERENTIAL DRIVE PINION PRELOAD
INSPECT TOTAL PRELOAD
INSPECT RUNOUT OF REAR DIFFERENTIAL CASE SUB-ASSEMBLY
Rear Differential Carrier (For 2Ad-Fhv) -- Inspection |
1. INSPECT RUNOUT OF DIFFERENTIAL RING GEAR |
Set the dial indicator perpendicular to the end of the ring gear face.
Rotate the ring gear and measure the backlash.
- Maximum runout:
- 0.05 mm (0.0020 in.)
If the runout exceeds the specified maximum value, remove the ring gear and check the runout of the differential case.
2. INSPECT DIFFERENTIAL RING GEAR BACKLASH |
While holding the rear drive pinion companion flange, rotate the ring gear and measure the backlash.
- Backlash:
- 0.08 to 0.13 mm (0.0031 to 0.0051 in.)
If the backlash is not within the specified range, adjust the backlash or repair as necessary.
3. INSPECT TOOTH CONTACT BETWEEN RING GEAR AND DRIVE PINION |
Coat 3 or 4 teeth at the 3 different positions on the ring gear with Prussian blue.
Rotate the ring gear in both directions.
Inspect the tooth contact pattern.
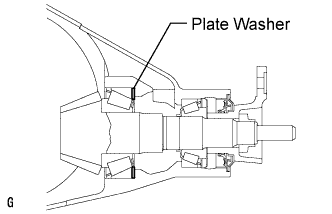
|
If the teeth are not contacting properly, use the following table to select a proper plate washer for correction.
- HINT:
- If the contact pattern is face contact or flank contact, tooth contact may be adjustable while keeping the backlash within the specified range.
- If the thickness of the drive pinion washer has been changed, adjust the backlash and measure the total preload.
Washer thicknessThickness mm (in.)
| No.
| Thickness mm (in.)
| No.
| Thickness mm (in.)
| No.
|
1.87 (0.0736)
| 87
| 2.01 (0.0791)
| 01
| 2.15 (0.0846)
| 15
|
1.88 (0.0740)
| 88
| 2.02 (0.0795)
| 02
| 2.16 (0.0850)
| 16
|
1.89 (0.0744)
| 89
| 2.03 (0.0799)
| 03
| 2.17 (0.0854)
| 17
|
1.90 (0.0748)
| 90
| 2.04 (0.0803)
| 04
| 2.18 (0.0858)
| 18
|
1.91 (0.0752)
| 91
| 2.05 (0.0807)
| 05
| 2.19 (0.0862)
| 19
|
1.92 (0.0756)
| 92
| 2.06 (0.0811)
| 06
| 2.20 (0.0866)
| 20
|
1.93 (0.0760)
| 93
| 2.07 (0.0815)
| 07
| 2.21 (0.0870)
| 21
|
1.94 (0.0764)
| 94
| 2.08 (0.0819)
| 08
| 2.22 (0.0874)
| 22
|
1.95 (0.0768)
| 95
| 2.09 (0.0823)
| 09
| 2.23 (0.0878)
| 23
|
1.96 (0.0772)
| 96
| 2.10 (0.0827)
| 10
| 2.24 (0.0882)
| 24
|
1.97 (0.0776)
| 97
| 2.11 (0.0831)
| 11
| 2.25 (0.0886)
| 25
|
1.98 (0.0780)
| 98
| 2.12 (0.0835)
| 12
| 2.26 (0.0890)
| 26
|
1.99 (0.0783)
| 99
| 2.13 (0.0839)
| 13
| 2.27 (0.0894)
| 27
|
2.00 (0.0787)
| 00
| 2.14 (0.0843)
| 14
| 2.28 (0.0898)
| 28
|
4. INSPECT DIFFERENTIAL SIDE GEAR BACKLASH |
Place a dial indicator on the tip of the pinion gear tooth at a right angle. Hold the side gear in the differential case and check that the backlash is 0 mm (0 in.).
If not, replace the rear differential case sub-assembly with a new one.
5. INSPECT DIFFERENTIAL SIDE GEAR BACKLASH |
Hold the differential case in a vise between aluminum plates.
- NOTICE:
- Do not overtighten the vise.
Place a dial indicator on the tip of the side gear tooth at a right angle. Hold the pinion gear in the differential case and check that the backlash is 0 mm (0 in.).
If not, replace the rear differential case sub-assembly with a new one.
6. INSPECT RUNOUT OF DIFFERENTIAL DRIVE PINION |
Using a dial indicator, measure the runout of the drive pinion shaft at a position 10 mm (0.39 in.) away from the end of the shaft.
- Maximum runout:
- 0.08 mm (0.0031 in.)
If the runout is greater than the maximum, replace the drive pinion and ring gear.
7. INSPECT DIFFERENTIAL DRIVE PINION PRELOAD |
Using SST and a torque wrench, measure the starting torque of the drive pinion. The backlash between the drive pinion and ring gear should allow enough movement of the drive pinion to allow this measurement to be performed. Make sure not to include the preload of the ring gear (differential case) in the measurement of the drive pinion preload.
- SST
- 09229-55010
- Drive pinion preload (at starting):
Specifications
| Preload
|
New bearing
| 1.22 to 1.80 N*m (12.4 to 18.4 kgf*cm, 10.8 to 15.9 in.*lbf)
|
Reused bearing
| 0.50 to 0.80 N*m (5.1 to 8.2 kgf*cm, 4.3 to 6.9 in.*lbf)
|
If the preload is not within the specified range, adjust the rear differential drive pinion preload or repair as necessary.
Using SST and a torque wrench, measure the preload with the teeth of the drive pinion and ring gear in contact.
- SST
- 09229-55010
- Total preload (at starting):
Grade: luxurySpecifications
| Preload
|
New bearing
| 1.92 to 3.89 N*m (19.6 to 39.7 kgf*cm, 17.0 to 34.4 in.*lbf)
|
Reused bearing
| 1.20 to 2.89 N*m (12.2 to 29.5 kgf*cm, 10.6 to 25.6 in.*lbf)
|
Grade: sportSpecifications
| Preload
|
New bearing
| 1.75 to 3.38 N*m (17.8 to 34.5 kgf*cm, 15.5 to 29.9 in.*lbf)
|
Reused bearing
| 1.03 to 2.38 N*m (10.5 to 24.3 kgf*cm, 9.1 to 21.1 in.*lbf)
|
If the preload is not within the specified range, adjust the total preload or repair as necessary.
9. INSPECT RUNOUT OF REAR DIFFERENTIAL CASE SUB-ASSEMBLY |
- HINT:
- Perform this procedure only when the runout of the differential ring gear exceeds the specified maximum value.
Install the differential case to the differential carrier.
- NOTICE:
- Do not damage the case bearing.
Using SST and a hammer, install the case bearing outer race on the ring gear tooth side.
- SST
- 09608-32010
09950-70010(09951-07200)
- HINT:
- Tap in the case bearing outer race until half of the side gear shaft snap ring groove of the differential carrier can be seen.
Install SST to the differential carrier.
- SST
- 09571-50010
Tighten the SST bolt (A) until the SST disc slightly touches the case bearing outer race.
Using SST and a hammer, install the case bearing outer race on the ring gear back surface side.
- SST
- 09608-32010
09950-70010(09951-07200)
- HINT:
- Tap in the case bearing outer race until it touches the case bearing inner race roller.
Using snap ring pliers, install the side gear shaft snap ring in the differential carrier on the ring gear back surface side.
Place a dial indicator on the differential case flange surface at a right angle.
Using a dial indicator, measure the differential case runout.
- Maximum runout:
- 0.05 mm (0.0020 in.)
If the runout is greater than the maximum, replace the rear differential case with a new one.
Using snap ring pliers, remove the side gear shaft snap ring on the ring gear back surface side.
Tighten the SST bolt to push out the ring gear back surface side case bearing outer race.
- SST
- 09571-50010
- NOTICE:
- Do not drop the case bearing outer race.
Remove the SST.
Raise the ring gear side of the differential case slightly to remove the ring gear tooth side case bearing outer race.
Remove the differential case from the differential carrier.
- NOTICE:
- Do not damage the case bearing.