Land Cruiser URJ200 URJ202 GRJ200 VDJ200 - 1GR-FE ENGINE MECHANICAL
ENGINE ASSEMBLY - INSTALLATION
1. INSTALL FRONT NO. 2 ENGINE MOUNTING BRACKET LH |
Install the front No. 2 engine mounting bracket LH with the bolt.
- Torque:
- 32 N*m{ 326 kgf*cm, 24 ft.*lbf}
2. INSTALL ENGINE HANGER |

Install 2 engine hangers with 4 bolts as shown in the illustration.
- Torque:
- 33 N*m{ 337 kgf*cm, 24 ft.*lbf}
*1 | No. 1 Engine Hanger |
*2 | No. 2 Engine Hanger |
- HINT:
No. 1 Engine Hanger | 12281-31110 |
No. 2 Engine Hanger | 12282-31140 |
Bolt | 91671-C0830 |
3. REMOVE ENGINE STAND |
Attach an engine sling device and hang the engine with a chain block.
Lift the engine and remove it from the engine stand.
- NOTICE:
Place the engine onto a work bench.
4. INSTALL ENGINE ASSEMBLY |
Slowly lower the engine into the engine compartment.

Install the front engine mounting insulator LH with the 2 bolts and nut.
- Torque:
- for bolt:
- 79 N*m{ 806 kgf*cm, 58 ft.*lbf}
- for nut:
- 72 N*m{ 734 kgf*cm, 53 ft.*lbf}
![]() | Bolt |
![]() | Nut |
Install the front engine mounting insulator RH with the 2 bolts and nut.
- Torque:
- for bolt:
- 79 N*m{ 806 kgf*cm, 58 ft.*lbf}
- for nut:
- 72 N*m{ 734 kgf*cm, 53 ft.*lbf}
Remove the 2 engine hangers and 4 bolts.
5. INSTALL DRIVE PLATE AND RING GEAR SUB-ASSEMBLY (for Automatic Transmission) |

Using SST, hold the crankshaft.
- SST
- 09213-54015(91651-60855)
09330-00021
Clean the bolts and their installation holes.
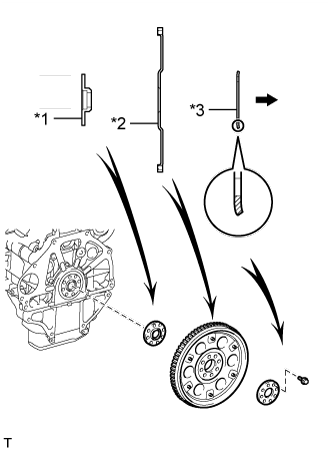
Install the front spacer, drive plate and rear spacer to the crankshaft.
*1 | Front Spacer |
*2 | Drive Plate and Ring Gear |
*3 | Rear Spacer |
![]() | Automatic Transmission Side |
- HINT:
- As the front spacer, the drive plate and ring gear, and the rear spacer are not reversible, be sure to install them in the direction shown in the illustration.
Apply adhesive to 2 or 3 threads at the end of the 8 new bolts.
- Adhesive:
- Toyota Genuine Adhesive 1324, Three Bond 1324 or equivalent
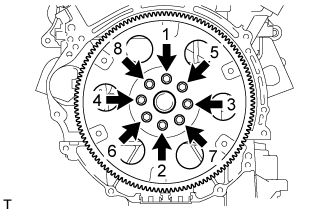
Uniformly install and tighten the 8 bolts in several steps in the sequence shown in the illustration.
- Torque:
- 83 N*m{ 846 kgf*cm, 61 ft.*lbf}
- NOTICE:
- Do not start the engine for at least 1 hour after installing.
6. INSTALL FLYWHEEL SUB-ASSEMBLY (for Manual Transmission) |

Using SST, hold the crankshaft.
- SST
- 09213-54015(91651-60855)
09330-00021
Clean the bolts and their installation holes.
Temporarily install the flywheel with 8 new bolts.
Install and tighten the 8 bolts uniformly in several steps.
- Torque:
- 30 N*m{ 306 kgf*cm, 22 ft.*lbf}
Mark the top of the bolts with paint.
Tighten the 8 bolts 90° in the same sequence.
Check that the paint marks are now at a 90° angle to the top.
7. INSTALL CLUTCH DISC ASSEMBLY (for Manual Transmission) |
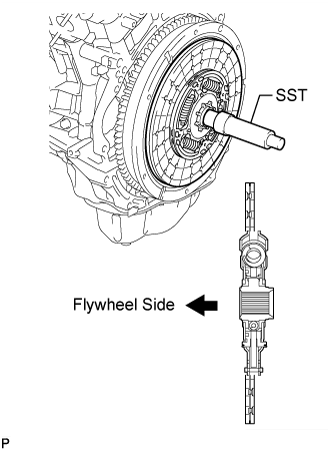
Insert SST into the clutch disc, then insert the clutch disc into the flywheel.
- SST
- 09301-00110
- NOTICE:
- Take care not to insert the clutch disc in the wrong direction.
8. INSTALL CLUTCH COVER ASSEMBLY (for Manual Transmission) |
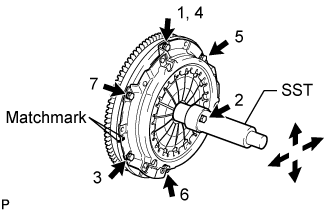
Align the matchmark on the clutch cover with the one on the flywheel.
In the order shown in the illustration, temporarily install the 6 bolts starting from the bolt located near the knock pin on the top.
Check that the disc is in the center by lightly moving SST up and down, and left and right.
- SST
- 09301-00110
Evenly tighten the bolts by following the order shown in the illustration.
- Torque:
- 19 N*m{ 195 kgf*cm, 14 ft.*lbf}
9. INSPECT AND ADJUST CLUTCH COVER ASSEMBLY (for Manual Transmission) |

Using a dial indicator with a roller instrument, check the diaphragm spring tip alignment.
- Maximum Misalignment:
- 1.3 mm (0.0512 in.)

If the alignment is not as specified, adjust the diaphragm spring tip alignment using SST.
- SST
- 09333-00013
10. CONNECT NO. 1 OIL COOLER HOSE TUBE SUB-ASSEMBLY |
Connect the cooler hose tube with the 2 bolts.
- Torque:
- 14 N*m{ 143 kgf*cm, 10 ft.*lbf}
11. INSTALL REAR NO. 1 ENGINE MOUNTING INSULATOR |
Install the rear No. 1 engine mounting insulator to the transmission with the 4 bolts.
- Torque:
- 59 N*m{ 602 kgf*cm, 44 ft.*lbf}
12. INSTALL MANUAL TRANSMISSION ASSEMBLY (for Manual Transmission) |
()
13. INSTALL AUTOMATIC TRANSMISSION ASSEMBLY (for Automatic Transmission) |
()
14. CONNECT NO. 1 AND NO. 2 FUEL PIPE |
Connect the No. 1 and No. 2 fuel pipes ().
15. INSTALL COOLER COMPRESSOR ASSEMBLY |

Install the cooler compressor with the 3 bolts.
- Torque:
- 24.5 N*m{ 250 kgf*cm, 18 ft.*lbf}
- HINT:
- Tighten the bolts in the order shown in the illustration.
Connect the connector.
16. CONNECT SUCTION HOSE SUB-ASSEMBLY |

Remove the attached vinyl tape from the hose.
Sufficiently apply compressor oil to a new O-ring and the fitting surface of the cooler compressor.
- Compressor oil:
- ND-OIL 8 or equivalent
Install the O-ring to the suction hose.
Connect the suction hose to the cooler compressor with the 2 bolts.
- Torque:
- for bolt A:
- 9.8 N*m{ 100 kgf*cm, 87 ft.*lbf}
- for bolt B:
- 24.5 N*m{ 250 kgf*cm, 18 ft.*lbf}
17. CONNECT NO. 1 COOLER REFRIGERANT DISCHARGE HOSE |

Remove the attached vinyl tape from the hose.
Sufficiently apply compressor oil to a new O-ring and the fitting surface of the cooler compressor.
- Compressor oil:
- ND-OIL 8 or equivalent
Install the O-ring to the cooler refrigerant discharge hose.
Connect the cooler refrigerant discharge hose to the cooler compressor with the bolt.
- Torque:
- 9.8 N*m{ 100 kgf*cm, 87 in.*lbf}
18. INSTALL GENERATOR ASSEMBLY |
Install the generator bracket to the generator with the bolt.
- Torque:
- 20 N*m{ 204 kgf*cm, 15 ft.*lbf}
Install the generator with the 2 bolts.
- Torque:
- 43 N*m{ 438 kgf*cm, 32 ft.*lbf}
Connect the generator bracket with the bolt.
- Torque:
- 20 N*m{ 204 kgf*cm, 15 ft.*lbf}
Connect the wire harness clamp bracket with the bolt.
- Torque:
- 8.0 N*m{ 82 kgf*cm, 71 in.*lbf}
Connect the generator wire to terminal B with the nut.
- Torque:
- 9.8 N*m{ 100 kgf*cm, 87 in.*lbf}
Close the terminal cap.
Connect the generator connector.
19. CONNECT VANE PUMP ASSEMBLY |
Connect the vane pump with the 2 bolts.
- Torque:
- 21 N*m{ 214 kgf*cm, 15 ft.*lbf}
Attach the wire harness clamp.
Connect the connector.
20. CONNECT WATER HOSE SUB-ASSEMBLY |
Connect the water hoses.
21. INSTALL EXHAUST MANIFOLD SUB-ASSEMBLY LH |
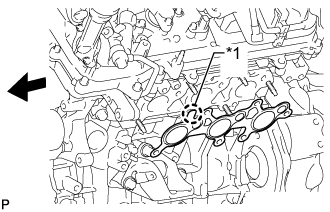
Install a new gasket to the cylinder head.
*1 | Protrusion |
![]() | Front |
- NOTICE:
- Be careful of the installation direction.
Temporarily install the manifold with 6 new nuts.

Tighten the 6 nuts in the sequence shown in the illustration.
- Torque:
- 21 N*m{ 214 kgf*cm, 15 ft.*lbf}
*A | w/ Secondary Air Injection System |
*B | w/o Secondary Air Injection System |
Connect the air fuel ratio sensor connector.
22. INSTALL NO. 2 EXHAUST MANIFOLD HEAT INSULATOR |
Install the heat insulator with the 3 bolts.
- Torque:
- 13 N*m{ 133 kgf*cm, 10 ft.*lbf}
23. INSTALL NO. 2 AIR TUBE (w/ Secondary Air Injection System) |
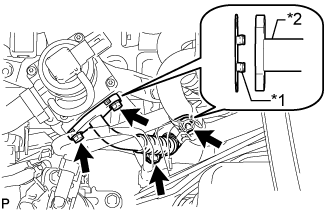
Install 2 new gaskets.
*1 | Claw |
*2 | No. 2 Air Tube |
- NOTICE:
- Make sure the gasket's claws are not caught between the No. 2 emission control valve set and No. 2 air tube.
Install the No. 2 air tube with the 2 bolts and 2 nuts.
- Torque:
- 10 N*m{ 102 kgf*cm, 7 ft.*lbf}
24. INSTALL NO. 2 MANIFOLD STAY |
Install the manifold stay with the 3 bolts.
- Torque:
- 40 N*m{ 408 kgf*cm, 30 ft.*lbf}
25. INSTALL EXHAUST MANIFOLD SUB-ASSEMBLY RH |

Install a new gasket to the cylinder head.
*1 | Protrusion |
![]() | Front |
- NOTICE:
- Be careful of the installation direction.
Temporarily install the manifold with 6 new nuts.

Tighten the 6 nuts in the sequence shown in the illustration.
- Torque:
- 21 N*m{ 214 kgf*cm, 15 ft.*lbf}
*A | w/ Secondary Air Injection System |
*B | w/o Secondary Air Injection System |
Connect the air fuel ratio sensor connector.
26. INSTALL NO. 1 EXHAUST MANIFOLD HEAT INSULATOR |
Install the heat insulator with the 3 bolts.
- Torque:
- 13 N*m{ 133 kgf*cm, 10 ft.*lbf}
27. CONNECT NO. 2 STEERING INTERMEDIATE SHAFT |
28. INSTALL AIR TUBE (w/ Secondary Air Injection System) |
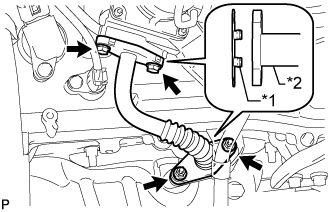
Install 2 new gaskets.
*1 | Claw |
*2 | Air Tube |
- NOTICE:
- Make sure the gasket's claws are not caught between the No. 1 emission control valve set and air tube.
Install the air tube with the 2 bolts and 2 nuts.
- Torque:
- 10 N*m{ 102 kgf*cm, 7 in.*lbf}
29. INSTALL MANIFOLD STAY |
Install the No. 2 manifold stay with the 3 bolts.
- Torque:
- 40 N*m{ 408 kgf*cm, 30 ft.*lbf}
30. INSTALL FRONT FENDER APRON TRIM PACKING D |
Install the front fender apron trim packing D with the 4 clips.
31. INSTALL FRONT FENDER APRON TRIM PACKING C |
Install the front fender apron trim packing C with the 4 clips.
32. INSTALL FRONT FENDER APRON TRIM PACKING B |
w/ KDSS:
Install the front fender apron trim packing B with the 3 clips.
w/o KDSS:
Install the front fender apron trim packing B with the 4 clips.
33. INSTALL FRONT FENDER APRON TRIM PACKING A |
Install the front fender apron trim packing A with the 3 clips.
34. INSTALL FRONT EXHAUST PIPE ASSEMBLY |
Install a new gasket and the front exhaust pipe to the exhaust manifold RH with 2 new nuts.
- Torque:
- 54 N*m{ 554 kgf*cm, 40 ft.*lbf}
Connect the heated oxygen sensor connector.
35. INSTALL HEATED OXYGEN SENSOR (for Bank 2 Sensor 2) |

Temporarily install the sensor to the exhaust pipe by hand.

Using SST, tighten the sensor.
- SST
- 09224-00010
- Torque:
- without SST:
- 44 N*m{ 449 kgf*cm, 32 ft.*lbf}
- with SST:
- 40 N*m{ 408 kgf*cm, 30 ft.*lbf}
- HINT:
36. INSTALL FRONT NO. 2 EXHAUST PIPE ASSEMBLY |
Install a new gasket and the front No. 2 exhaust pipe to the exhaust manifold LH with 2 new nuts.
- Torque:
- 54 N*m{ 554 kgf*cm, 40 ft.*lbf}

Connect the heated oxygen sensor connector.
- HINT:
- Hook the wire harness to the bracket.
37. INSTALL CENTER EXHAUST PIPE ASSEMBLY |

Check the free length.
Using a vernier caliper, measure the free length of the compression spring.
- Minimum free length:
- 43 mm (1.693 in.)
If the free length is less than the minimum, replace the compression spring.
Connect the center exhaust pipe to the 3 exhaust pipe supports.
Install 2 new gaskets to the front exhaust pipe and front No. 2 exhaust pipe.
Install the center exhaust pipe with the 4 bolts and 2 compression springs.
- Torque:
- for center exhaust pipe and front exhaust pipe:
- 43 N*m{ 438 kgf*cm, 32 ft.*lbf}
- for center exhaust pipe and front No. 2 exhaust pipe:
- 48 N*m{ 489 kgf*cm, 35 ft.*lbf}
38. INSTALL TAILPIPE ASSEMBLY |
Install the tailpipe to the 2 exhaust pipe supports.
Set a new gasket to the center exhaust pipe.

Connect the tailpipe to the center pipe with a new clamp.
- Torque:
- 32 N*m{ 326 kgf*cm, 24 ft.*lbf}
- HINT:
- Install the clamp within the angle range shown in the illustration.
39. INSTALL HEATED OXYGEN SENSOR (for Bank 1 Sensor 2) |

Temporarily install the sensor to the exhaust pipe by hand.

Using SST, tighten the sensor.
- SST
- 09224-00010
- Torque:
- without SST:
- 44 N*m{ 449 kgf*cm, 32 ft.*lbf}
- with SST:
- 40 N*m{ 408 kgf*cm, 30 ft.*lbf}
- HINT:

Connect the sensor connector.
40. CONNECT ENGINE WIRE |

w/ Secondary Air Injection System:
Attach the clamp and connect the air pump connector.

Attach the clamp and connect the power steering switch connector.
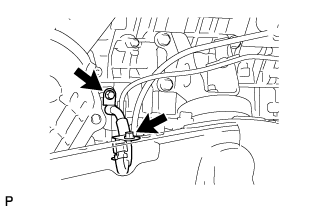
w/ Winch:
Install the winch ground wire with the 2 bolts.
- Torque:
- 19 N*m{ 196 kgf*cm, 14 ft.*lbf}

Attach the 2 clamps and connect the connector.

Install the ground wire with the bolt and attach the wire harness clamp.
- Torque:
- 8.4 N*m{ 86 kgf*cm, 74 in.*lbf}
Connect the cable to the positive (+) battery terminal.
Connect the wire to the positive (+) battery cable with the nut.
- Torque:
- 7.5 N*m{ 76 kgf*cm, 66 in.*lbf}
Connect the wire and 2 clips to the engine room junction block with the nut.
- Torque:
- 7.5 N*m{ 76 kgf*cm, 66 in.*lbf}
Connect the 2 clips and 2 connectors to the engine room junction block.
w/ Secondary Air Injection System:
Attach the clamp and connect the 2 air injection control driver connectors.
Connect the ground wire to the bracket with the bolt.
- Torque:
- 5.0 N*m{ 51 kgf*cm, 44 in.*lbf}
Install the engine room relay block cover.
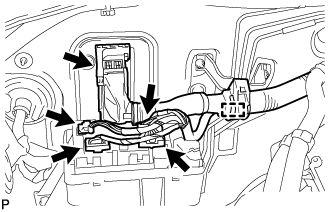
Connect the 4 connectors to the junction block.
Attach the wire harness clamp.
Connect the ECM connector ().
Install the junction block cover.
41. INSTALL INTAKE AIR SURGE TANK |
Install a new gasket to the intake air surge tank.
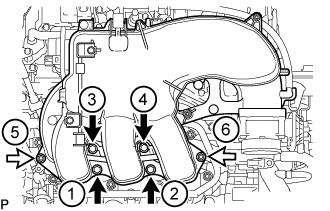
Install the intake air surge tank with the 4 bolts and 2 nuts in the order shown in the illustration.
- Torque:
- 28 N*m{ 286 kgf*cm, 21 ft.*lbf}
![]() | Bolt |
![]() | Nut |
Install the throttle body bracket with the 2 bolts.
- Torque:
- 21 N*m{ 214 kgf*cm, 15 ft.*lbf}
Install the No. 1 surge tank stay with the 2 bolts.
- Torque:
- 21 N*m{ 214 kgf*cm, 15 ft.*lbf}
Attach the wire harness clamp.
Install the bracket with the bolt and attach the 2 wire harness clamps.
- Torque:
- 8.0 N*m{ 82 kgf*cm, 71 in.*lbf}
Install the No. 2 surge tank stay with the 2 bolts.
- Torque:
- 21 N*m{ 214 kgf*cm, 15 ft.*lbf}
for Manual Transmission:
Connect the clutch flexible hose bracket with the nut.
- Torque:
- 20 N*m{ 204 kgf*cm, 15 ft.*lbf}

Connect the No. 1 PCV hose.
*a | Front |
*b | RH |
- HINT:
- Connect the No. 1 PCV hose so that the direction of the hose clamp is as indicated in the illustration.
Connect the No. 1 vacuum switching valve connector.
Connect the purge line hose.
Connect the throttle body connector.
Connect the No. 4 water by-pass hose.
Connect the No. 5 water by-pass hose.
42. INSTALL AIR TUBE ASSEMBLY (w/ Secondary Air Injection System) |
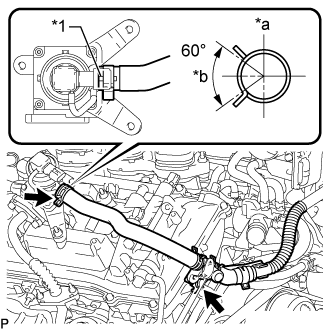
for Bank 1 Side:
Align the paint mark with the projection and connect the air tube assembly to the emission control valve set.
*1 | Paint Mark |
*a | Top |
*b | RH Side |
- HINT:
- Make sure the direction of the hose clamp is as shown in the illustration.
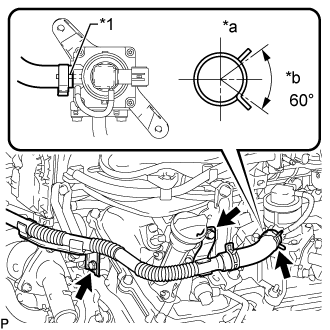
for Bank 2 Side:
Align the paint mark with the projection and connect the air tube assembly to the No. 2 emission control valve set.
*1 | Paint Mark |
*a | Top |
*b | LH Side |
- HINT:
- Make sure the direction of the hose clamp is as shown in the illustration.
Install the 3 bolts.
- Torque:
- 10 N*m{ 102 kgf*cm, 7 ft.*lbf}
Connect the No. 3 air hose.
43. INSTALL AIR CLEANER CASE SUB-ASSEMBLY |
Install the air cleaner case with the 3 bolts.
- Torque:
- 5.0 N*m{ 51 kgf*cm, 44 in.*lbf}
Install the air cleaner filter element.
44. INSTALL AIR CLEANER CAP AND HOSE |
Install the air cleaner cap and hose.
Install the air cleaner cap and hose with the bolt and fasten the 4 hook clamps.
- Torque:
- 5.0 N*m{ 51 kgf*cm, 44 in.*lbf}
Tighten the clamp.
- Torque:
- 2.5 N*m{ 25 kgf*cm, 22 in.*lbf}
Attach the clamp and connect the ventilation hose, vacuum hose and mass air flow meter connector.
45. INSTALL RADIATOR ASSEMBLY |
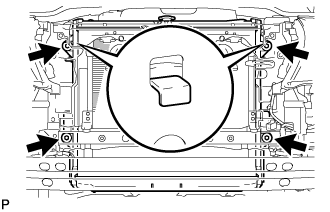
Set the radiator bracket hooks into the radiator support holes.
Install the radiator with the 4 bolts.
- Torque:
- 18 N*m{ 184 kgf*cm, 13 ft.*lbf}
46. CONNECT OUTLET OIL COOLER HOSE (for Automatic Transmission) |
Connect the cooler hose.
47. CONNECT INLET OIL COOLER HOSE (for Automatic Transmission) |
Connect the cooler hose.
48. INSTALL FAN SHROUD |
Install the fan pulley to the water pump.
Place the shroud together with the coupling fan between the radiator and engine.
- NOTICE:
- Be careful not to damage the radiator core.
Temporarily install the fluid coupling fan to the water pump with the 4 nuts. Tighten the nuts as much as possible by hand.
- NOTICE:
- Match the paint marks on the heads of the water pump studs with the paint marks on the flange of the fluid coupling and install the fluid coupling.
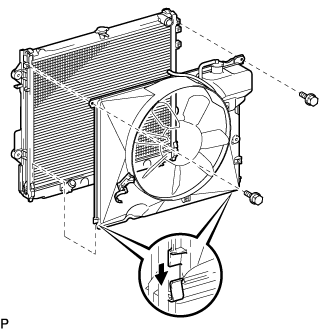
Attach the claws of the shroud to the radiator as shown in the illustration.
Install the shroud with the 2 bolts.
- Torque:
- 8.0 N*m{ 82 kgf*cm, 71 in.*lbf}
Connect the reservoir hose to the upper side of the radiator tank.
Install the fan and generator V-belt ().
Tighten the 4 nuts of the fluid coupling fan.
- Torque:
- 21 N*m{ 214 kgf*cm, 15 ft.*lbf}
49. CONNECT OIL COOLER TUBE (w/ Air Cooled Transmission Oil Cooler) |
Connect the oil cooler tube with the 2 bolts, and attach the claw to close the flexible hose clamp.
- Torque:
- 5.0 N*m{ 51 kgf*cm, 44 in.*lbf}
50. INSTALL NO. 2 RADIATOR HOSE |
Install the No. 2 radiator hose and attach the clamp.
51. INSTALL NO. 1 RADIATOR HOSE |
52. INSTALL RADIATOR SIDE DEFLECTOR LH |
Install the deflector with the 4 clips.
53. INSTALL RADIATOR SIDE DEFLECTOR RH (w/o Air Cooled Transmission Oil Cooler) |
Install the deflector with the 4 clips.
54. INSTALL TRANSMISSION OIL COOLER AIR DUCT (w/ Air Cooled Transmission Oil Cooler) |
Install the oil cooler air duct with the 4 bolts.
- Torque:
- 4.9 N*m{ 50 kgf*cm, 43 in.*lbf}
55. INSTALL V-BANK COVER |
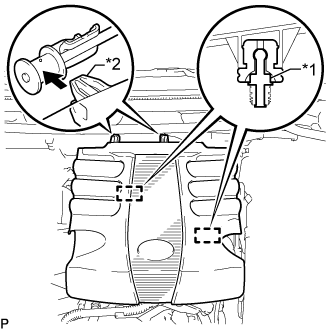
Attach the 2 V-bank cover hooks to the bracket. Then align the 2 V-bank cover grommets with the 2 pins and press down on the V-bank cover to attach the pins.
*1 | Pin |
*2 | Hook |
56. INSTALL FRONT BUMPER COVER |
57. INSTALL RADIATOR GRILLE |
w/ Wide View Front Monitor System:
Connect the connector.
Attach the 2 clips and 8 claws to install the radiator grille assembly.
Install the 3 screws.
58. INSTALL UPPER RADIATOR SUPPORT SEAL |
Install the radiator support seal with the 7 clips.
59. INSTALL NO. 2 ENGINE UNDER COVER |
Install the No. 2 engine under cover with the 2 bolts.
- Torque:
- 29 N*m{ 296 kgf*cm, 21 ft.*lbf}
60. INSTALL NO. 1 ENGINE UNDER COVER SUB-ASSEMBLY |
Install the No. 1 engine under cover with the 10 bolts.
- Torque:
- 29 N*m{ 296 kgf*cm, 21 ft.*lbf}
61. INSTALL FRONT FENDER SPLASH SHIELD SUB-ASSEMBLY LH |
Push in the clip to install the front fender splash shield sub-assembly LH.
Install the 3 bolts and screw.
62. INSTALL FRONT FENDER SPLASH SHIELD SUB-ASSEMBLY RH |
Push in the clip to install the front fender splash shield sub-assembly RH.
Install the 3 bolts and 2 screws.
63. INSTALL COWL TOP VENTILATOR LOUVER SUB-ASSEMBLY |
()
64. CONNECT CABLE TO NEGATIVE BATTERY TERMINAL |
- NOTICE:
- When disconnecting the cable, some systems need to be initialized after the cable is reconnected ().
65. ADD ENGINE OIL |
Add fresh oil.
- NOTICE:

- Do not allow engine oil to adhere to the moving parts of the belt tensioner, as this may cause malfunctions.
- If engine oil is on the location indicated by the arrow, replace the belt tensioner.
- Standard Engine Oil:
Oil Grade Oil Viscosity (SAE) API grade SL "Energy-Conserving", SM "Energy-Conserving", SN "Resource-Conserving" or ILSAC multigrade engine oil 5W-30
10W-30API grade SL, SM or SN multigrade engine oil 15W-40
20W-50
- Standard Engine Oil (for China):
Oil Grade Oil Viscosity (SAE) API grade SL "energy-conserving", SM "energy-conserving", SN "resource-conserving" or ILSAC multigrade engine oil 0W-20
5W-20
5W-30
10W-30API grade SL, SM or SN multigrade engine oil 15W-40
20W-50
- Standard Oil Capacity:
Item Specified Condition Drain and refill without oil filter change 5.6 liters (5.9 US qts, 4.9 Imp. qts) Drain and refill with oil filter change 6.1 liters (6.4 US qts, 5.4 Imp. qts) Dry fill 7.1 liters (7.5 US qts, 6.2 Imp. qts)
66. ADD ENGINE COOLANT |
Add engine coolant.
- Standard Capacity (for Manual transmission):
Item Specified Condition w/ Rear Heater 14.6 liters (15.4 US qts, 12.8 Imp. qts) w/o Rear Heater 11.7 liters (12.4 US qts, 10.3 Imp. qts)
- Standard capacity (for Automatic transmission):
- 11.2 liters (11.8 US qts, 9.9 Imp. qts)
- Standard Capacity (for China):
- 14.4 liters (15.2 US qts, 12.7 Imp. qts)
- NOTICE:
- Do not substitute plain water for engine coolant.
- HINT:
- TOYOTA vehicles are filled with TOYOTA SLLC at the factory. In order to avoid damage to the engine cooling system and other technical problems, only use TOYOTA SLLC or similar high quality ethylene glycol based non-silicate, non-amine, non-nitrite, non-borate coolant with long-life hybrid organic acid technology (coolant with long-life hybrid organic acid technology consists of a combination of low phosphates and organic acids).
Slowly pour coolant into the radiator reservoir until it reaches the F line.
Install the reservoir cap.
Press the No. 1 and No. 2 radiator hoses several times by hand, and then check the coolant level. If the coolant level is low, add coolant.
Install the radiator cap.
Set the air conditioning as follows while warming up the engine.
Item | Condition |
Fan speed | Any setting except off |
Temperature | Toward WARM |
Air conditioning switch | Off |
Start the engine and warm it up until the thermostat opens.
- HINT:
- The thermostat opening timing can be confirmed by pressing the No. 2 radiator hose by hand, and checking when the engine coolant starts to flow inside the hose.
Maintain the engine speed at 2000 to 2500 rpm.
- NOTICE:
Press the No. 1 and No. 2 radiator hoses several times by hand to bleed air.
- CAUTION:
Stop the engine, and wait until the engine coolant cools down to ambient temperature.
- CAUTION:
- Do not remove the radiator cap while the engine and radiator are still hot. Pressurized, hot engine coolant and steam may be released and cause serious burns.
Check that the coolant level is between the F and L lines.
If the coolant level is below the L line, repeat all of the procedures above.
If the coolant level is above the F line, drain coolant so that the coolant level is between the F and L lines.
67. INSPECT FOR FUEL LEAK |
Make sure that there are no fuel leaks after performing maintenance on the fuel system.
Connect the GTS to the DLC3.
Turn the ignition switch to ON and turn the GTS on.
- NOTICE:
- Do not start the engine.
Enter the following menus: Powertrain / Engine and ECT / Active Test / Control the Fuel Pump / Speed.
Check that there are no leaks from the fuel system.
If there are fuel leaks, repair or replace parts as necessary.
Turn the ignition switch off.
Disconnect the GTS from the DLC3.
68. INSPECT FOR COOLANT LEAK |
- CAUTION:
- To avoid being burned, do not remove the radiator reservoir cap while the engine and radiator are still hot. Thermal expansion may cause hot engine coolant and steam to blow out from the radiator.
Fill the radiator with engine coolant, and then attach a radiator cap tester.
Warm up the engine.
Using the radiator cap tester, increase the pressure inside the radiator to 123 kPa (1.3 kgf/cm2, 18 psi), and then check that the pressure does not drop.
If the pressure drops, check the hoses, radiator and engine water pump for leakage. If there are no signs or traces of external engine coolant leakage, check the heater core, cylinder block and head.
69. INSPECT FOR OIL LEAK |
Start the engine. Make sure that there are no oil leaks from the area that was worked on.
70. INSPECT FOR EXHAUST GAS LEAK |
71. CHECK ENGINE OIL LEVEL |
Warm up the engine, and then stop the engine and wait for 5 minutes.
Check that the engine oil level is between the low level and full level marks on the dipstick.
If low, check for leakage and add oil up to the full level mark.
- NOTICE:
- Do not fill engine oil above the full level mark.
- HINT:
- A certain amount of engine oil will be consumed while driving. In the following situations, oil consumption may increase, and engine oil may need to be refilled in between oil maintenance intervals.
- When judging the amount of oil consumption, keep in mind that the oil may have become diluted, making it difficult to judge the true level accurately.
72. CHARGE REFRIGERANT |
- SST
- 09985-20010(09985-02130,09985-02150,09985-02090,09985-02110,09985-02010,09985-02050,09985-02060,09985-02070)
Perform vacuum purging using a vacuum pump.
Charge refrigerant HFC-134a (R134a).
Condenser Core Thickness | Air Conditioning Type | Cool Box | Refrigerant Charging Amount |
22 mm (0.866 in.) | w/o Rear Cooler | w/ Cool Box | 870 +/-30 g (30.7 +/-1.1 oz.) |
w/o Cool Box | 870 +/-30 g (30.7 +/-1.1 oz.) | ||
w/ Rear Cooler | w/ Cool Box | 1010 +/-30 g (35.6 +/-1.1 oz.) | |
w/o Cool Box | 960 +/-30 g (33.9 +/-1.1 oz.) | ||
16 mm (0.630 in.) | w/o Rear Cooler | w/ Cool Box | 770 +/-30 g (27.2 +/-1.1 oz.) |
w/o Cool Box | 770 +/-30 g (27.2 +/-1.1 oz.) | ||
w/ Rear Cooler | w/ Cool Box | 970 +/-30 g (34.2 +/-1.1 oz.) | |
w/o Cool Box | 920 +/-30 g (32.5 +/-1.1 oz.) |
- NOTICE:
73. WARM UP ENGINE |
Warm up the engine at less than 1850 rpm for 2 minutes or more after charging the refrigerant.
- NOTICE:
- Be sure to warm up the compressor when turning the A/C switch is on after removing and installing the cooler refrigerant lines (including the compressor), to prevent damage to the compressor.
74. CHECK FOR REFRIGERANT GAS LEAK |
After recharging the refrigerant gas, check for refrigerant gas leakage using a halogen leak detector.
Perform the operation under these conditions:
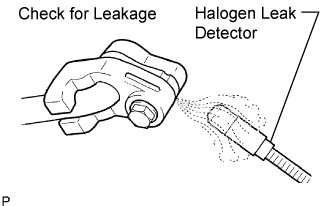
Using a halogen leak detector, check the refrigerant line for leakage.
If a gas leak is not detected on the drain hose, remove the blower motor control (blower resistor) from the cooling unit. Insert the halogen leak detector sensor into the unit and perform the test.
Disconnect the connector and wait for approximately 20 minutes. Bring the halogen leak detector close to the pressure switch and perform the test.
75. PERFORM RESET MEMORY (for Automatic Transmission) |
Perform the Reset Memory procedures ().
76. INSPECT IGNITION TIMING |
- NOTICE:
Warm up the engine.
When using the GTS:
Connect the GTS to the DLC3.
Enter the following menus: Powertrain / Engine and ECT / Data List / All Data / IGN Advance.
Inspect the ignition timing during idling.
- Standard ignition timing:
- 8 to 12° BTDC @ idle (transmission in neutral and A/C switch off)
Check that the ignition timing advances immediately when the engine speed is increased.
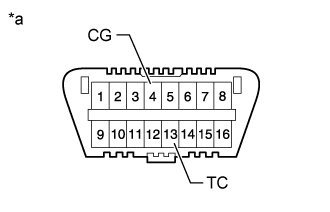
When not using the GTS:
Using SST, connect terminals 13 (TC) and 4 (CG) of the DLC3.
- SST
- 09843-18040
*a | Front view of DLC3 |
- NOTICE:
- Be sure not to improperly connect the terminals. This may damage the engine.
Connect the tester probe of a timing light to the wire of the ignition coil connector for the No. 1 cylinder.
- NOTICE:
Inspect the ignition timing during idling.
- Standard ignition timing:
- 8 to 12° BTDC @ idle (transmission in neutral and A/C switch off)
Remove SST from the DLC3.
Inspect the ignition timing during idling.
- Standard ignition timing:
- 7 to 24° BTDC @ idle (transmission in neutral and A/C switch off)
Disconnect the timing light from the engine.
77. INSPECT ENGINE IDLE SPEED |
- NOTICE:
Warm up the engine.
When using the GTS:
Connect the GTS to the DLC3.
Enter the following menus: Powertrain / Engine and ECT / Data List / All Data / Engine Speed.
Inspect the engine idle speed.
- Standard idle speed:
- 690 to 790 rpm (transmission in neutral and A/C switch off)

When not using the GTS:
Connect SST to terminal 9 (TAC) of the DLC3.
- SST
- 09843-18030
*a | Front view of DLC3 |
Race the engine at 2500 rpm for approximately 90 seconds.
Inspect the engine idle speed.
- Standard idle speed:
- 690 to 790 rpm (transmission in neutral and A/C switch off)
78. INSPECT CO/HC |
- HINT:
- This check is to determine whether or not the idle CO/HC concentration complies with regulations.
Start the engine.
Run the engine at 2500 rpm for approximately 180 seconds.
Insert the CO/HC meter testing probe at least 40 cm (1.31 ft) into the tailpipe during idling.
Immediately check the CO/HC concentration during idling and/or at 2500 rpm.
- HINT:
- When carrying out the 2 tests (idling and 2500 rpm), the measurement orders are prescribed by the applicable local regulations.
If the CO/HC concentration does not comply with regulations, perform troubleshooting in the order given below.
Check the air fuel ratio sensor operation () and heated oxygen sensor operation ().
See the table below for possible causes, and then inspect and correct the corresponding causes if necessary.
CO | HC | Symptom | Causes |
Normal | High | Rough idling | Faulty ignition: Incorrect timing Plugs are contaminated or shorted, or plug gaps are incorrect Incorrect valve clearance Leaky intake and exhaust valves Leaky cylinders |
Low | High | Rough idling (Fluctuating HC reading) | Vacuum leaks: Ventilation hoses Intake manifold Throttle body Lean mixture causing misfire |
High | High | Rough idle (Black smoke from exhaust) | Restricted air filter Plugged PCV valve Faulty SFI system: Faulty pressure regulator Defective engine coolant temperature sensor Faulty mass air flow meter Faulty ECM Faulty injectors Faulty throttle position sensor |
79. INSTALL HOOD SUB-ASSEMBLY |
Install the hood with the 4 bolts.
- Torque:
- 18 N*m{ 178 kgf*cm, 13 ft.*lbf}
80. INSPECT HOOD SUB-ASSEMBLY |
Check that the clearance measurements of areas A to C are within the standard range.
- Standard Measurement:
Area Specified Condition A (Reference) 2.3 to 5.3 mm (0.0906 to 0.209 in.) B 2.0 to 5.0 mm (0.0787 to 0.197 in.) C -1.5 to 1.5 mm (-0.0591 to 0.0591 in.)
81. ADJUST HOOD SUB-ASSEMBLY |
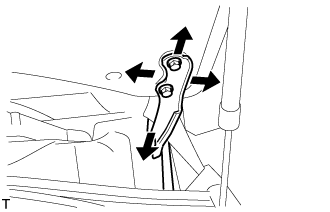
Adjust the hood position.
Loosen the 4 hinge bolts of the hood.
Move the hood and adjust the clearance between the hood and front fender.
Tighten the 4 hinge bolts of the hood after the adjustment.
- Torque:
- 13 N*m{ 133 kgf*cm, 10 ft.*lbf}

Adjust the cushion rubber so that the height of the hood and fender are aligned.
- HINT:
- Raise or lower the hood front end by turning the cushion rubber.
Adjust the hood lock.

Using a screwdriver, remove the hood lock nut cap as shown in the illustration.
- HINT:
- Tape the screwdriver tip before use.

Loosen the 2 bolts and hood lock nut.
Adjust the hood lock position so that the striker can enter it smoothly.
Tighten the bolts and nut after the adjustment.
- Torque:
- 5.5 N*m{ 56 kgf*cm, 49 in.*lbf}
Install a new cap.
82. INSPECT RESERVOIR TANK ENGINE COOLANT LEVEL |
The engine coolant should be between the L and F lines when the engine is cold.
If the engine coolant is below the L line, check for leakage and add TOYOTA Super Long Life Coolant (SLLC) or similar high quality ethylene glycol based non-silicate, non-amine, non-nitrite, non-borate coolant with long-life hybrid organic acid technology to the F line.
- NOTICE:
- Do not substitute plain water for engine coolant.