Lexus IS250 IS220d GSE20 ALE20 - ENGINE HOOD / DOOR
HOOD LOCK CONTROL CABLE ASSEMBLY - INSTALLATION
1. INSTALL HOOD LOCK CONTROL CABLE ASSEMBLY (for LHD) |
Pass the cable into the engine compartment.
Area | Part Name | Area | Part Name |
A | Hood lock control cable | E | Wire harness |
B | Stopper | F | Wire harness protector |
C | Grommet | G | Clamp |
D | Hood lock cable cover | - | - |
Pass the cable rear side through the grommet until the cable stopper is attached to the grommet.
Pass the cable front side through the upper radiator support.
2. INSTALL HOOD LOCK CONTROL CABLE ASSEMBLY (for RHD) |
Pass the cable into the engine compartment.
Area | Part Name | Area | Part Name |
A | Hood lock control cable | D | Hood lock cable cover |
B | Stopper | E | Wire harness |
C | Grommet | F | Clamp |
Pass the cable rear side through the grommet until the cable stopper is attached to the grommet.
Pass the cable front side through the upper radiator support.
3. INSTALL HOOD LOCK CONTROL LEVER SUB-ASSEMBLY (for LHD) |
Install the hood lock control lever and connect the hood lock control cable.
Area | Part Name | Area | Part Name |
A | Hood lock control cable | C | Junction block |
B | Parking brake cable | D | Clutch pedal |
Attach the 3 claws.
4. INSTALL HOOD LOCK CONTROL LEVER SUB-ASSEMBLY (for RHD) |

Install the hood lock control lever and connect the hood lock control cable.
Area | Part Name |
A | Hood lock control cable |
B | Accelerator pedal |
C | Wire harness |
Attach the 3 claws.
5. INSTALL HOOD LOCK ASSEMBLY |

Apply MP grease to the sliding areas of the lock.

Connect the hood lock control cable and connector.

Install the hood lock assembly with the 2 bolts and nut.
- Torque:
- 8.0 N*m{ 82 kgf*cm, 71 in.*lbf}
Install a new hood lock nut cap.
6. INSTALL HOOD LOCK CONTROL CABLE COVER |

Attach the claw and install the hood lock control cable cover.
Install the 3 screws.
7. INSTALL LOW PITCHED HORN ASSEMBLY |

Install the low pitched horn with the bolt.
- Torque:
- 19 N*m{ 194 kgf*cm, 14 ft.*lbf}
Connect the connector.
8. INSPECT HOOD SUB-ASSEMBLY |
Check that the clearance measurements of areas A to D are within each standard range.
- Standard clearance:
Area Measurement A 2.2 to 5.2 mm (0.087 to 0.205 in.) B -0.6 to 2.4 mm (-0.024 to 0.095 in.) C 2.2 to 5.2 mm (0.087 to 0.205 in.) D -1.3 to 1.7 mm (-0.051 to 0.067 in.)
9. ADJUST HOOD SUB-ASSEMBLY |
Horizontally and vertically adjust the hood.

Disengage the 2 clamps and claw, and remove the hood hinge cover LH.

Disengage the 2 clamps, and remove the hood hinge cover RH.

Loosen the hood's 4 hinge bolts.
Move the hood and adjust the clearance between the hood and front fender.
Tighten the hood's 4 hinge bolts after the adjustment.
- Torque:
- 13 N*m{ 133 kgf*cm, 10 ft.*lbf}
Adjust the height of the hood front end using the cushion rubber.

Adjust the cushion rubber so that the height of the hood and fender are aligned.
- HINT:
- Raise or lower the hood's front end by turning the cushion rubber.
Adjust the hood lock.

Using a screwdriver, remove the hood lock nut cap as shown in the illustration.
- HINT:
- Tape the screwdriver tip before use.

Loosen the 2 bolts and hood lock nut.
Tighten the bolts and nut after the adjustment.
- Torque:
- 8.0 N*m{ 82 kgf*cm, 71 in.*lbf}
Adjust the hood lock position so that the striker can enter it smoothly.
Install a new cap.
10. INSTALL MILLIMETER WAVE RADAR SENSOR ASSEMBLY (w/ Dynamic Radar Cruise Control System) |
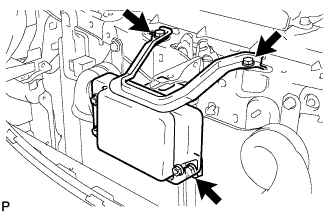
Install the millimeter wave radar sensor with the 3 bolts.
- Torque:
- 5.5 N*m{ 56 kgf*cm, 49 in.*lbf}
Connect the connector.
11. INSTALL FRONT BUMPER ASSEMBLY |
12. INSTALL FRONT UPPER FENDER PROTECTOR |
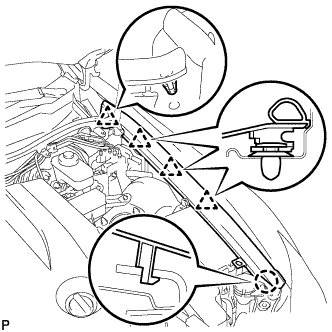
Engage the claw and the 3 clips, then install the front upper fender protector LH.
Engage the clip on the rubber portion of the cowl top ventilator louver sub-assembly to the front upper fender protector LH.
13. INSTALL ENGINE ROOM SIDE COVER (for 4GR-FSE) |
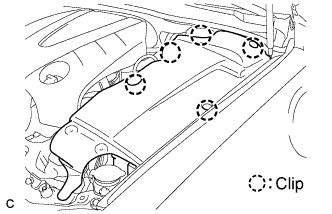
Install the side cover with the 5 clips.
14. INSTALL ENGINE ROOM SIDE COVER (for 2AD-FHV) |
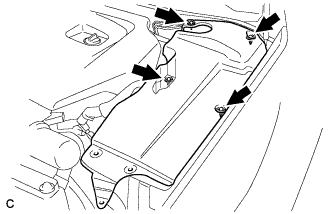
Install the side cover with the 4 clips.
15. INSTALL COOL AIR INTAKE DUCT SEAL |
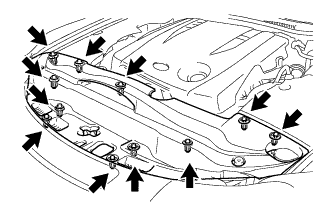
Install the intake duct seal with the 11 clips.
16. ADJUST MILLIMETER WAVE RADAR SENSOR ASSEMBLY (w/ Dynamic Radar Cruise Control System) |

- CAUTION:
- Exposure to radio frequency emissions is hazardous to your health. It is hazardous to your health to be within 20 cm (7.9 in.) of the device's radio frequency aperture.
- NOTICE:
Before adjusting the radar beam axis, prepare the vehicle as follows:
Check the tire pressure and adjust it if necessary.
Remove all excess weight from the vehicle (luggage, heavy objects, etc. ).
Check and adjust the vertical direction of the radar sensor.
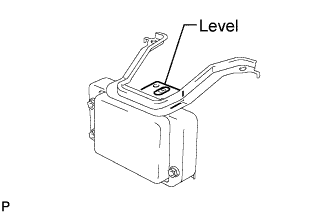
Remove dust, oil, and foreign matter from the radar sensor's level rack.
Set a level on the radar sensor's level rack.
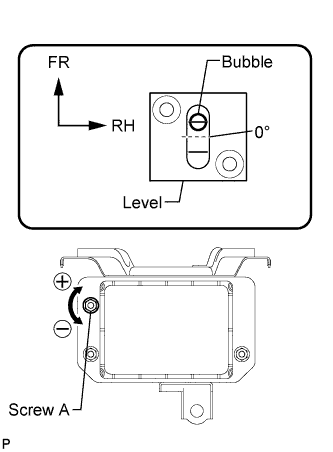
Check that the air bubble is within the red frame on the level.
- OK:
- The air bubble is within the red frame on the level.
If the bubble is not within the red frame, use a hexagon wrench to adjust screw A until the air bubble is within the red frame.
- HINT:
- Result:
Adjustment Direction Adjustment Procedure Adjustment Angle Vertical adjustment Upward direction: Turn screw A to negative (-) sideDownward direction: Turn screw A to positive (+) sideApprox. 1.0° per turn
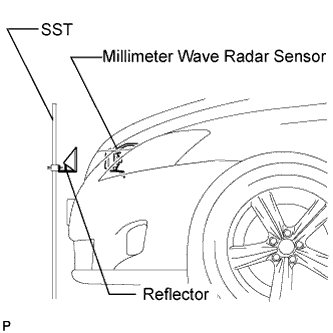
Adjust the reflector height.
Adjust the reflector so that the center of the SST reflector is the same height as the millimeter wave radar sensor.
- SST
- 09870-60000(09870-60010,09870-60040)
- HINT:
- Prepare a 10 m (32.81 ft) string, a string with a sharp-pointed weight (plumb bob), and a 5 m (16.41 ft) tape measure.
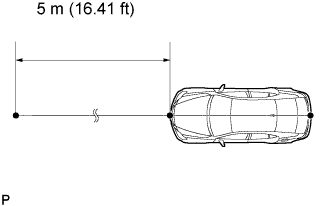
Place the reflector.
Hang the string (with weight) from the center of the vehicle's rear emblem. Mark the vehicle's rear center point on the ground. Repeat the same procedure for the front of the vehicle.
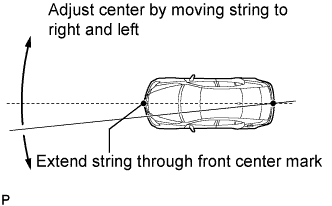
Set one end of the 10 m (32.82 ft) string on the vehicle's rear center point. Run the string over the vehicle's front center point to a position 5 m (16.41 ft) beyond the vehicle front center point, as shown in the illustration. Mark the 5 m (16.41 ft) position.
Using a tape measure, measure 12 mm (0.47 in.) to the left of the 5 m (16.41 ft) position. Place the reflector at that position.
- NOTICE:
- Perform the operation as precisely as possible.
Adjust the radar beam axis.
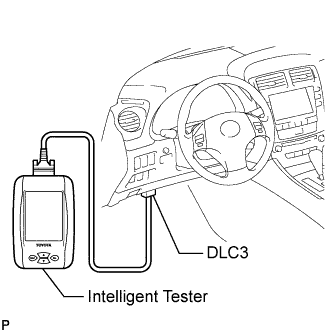
Connect the intelligent tester to the DLC3.
Turn the engine switch on (IG).
Turn the intelligent tester main switch on, and turn the cruise control main switch on.
- HINT:
- If an error message is displayed on the screen, initialization of the distance control ECU may not be completed. Initialize the distance control ECU
Check and adjust the horizontal direction of the radar sensor.
Check that the divergence of the radar beam axis is 0° .
- Standard:
- 0° (Both right and left)
- If the axis is not as specified, use a hexagon wrench to adjust screw B until the divergence of the radar beam axis is 0°.
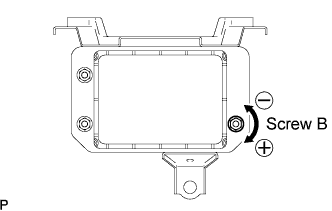
Based on the measured divergence of the beam axis, turn and adjust screw B for horizontal adjustment of the millimeter wave radar sensor using a hexagon wrench.
- Result:
Adjustment Direction Adjustment Procedure Adjustment Angle Horizontal adjustment Right direction: Turn screw B to positive (+) side.Left direction: Turn screw B to negative (-) side.Approx. 0.33° per turn
- HINT:
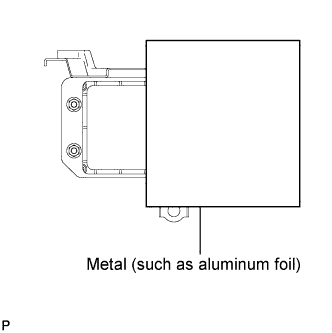
Reset the radar sensor's driving learning values. Prepare a type of metal that can block radio waves, such as aluminum foil. Cover the radar sensor's left half with the aluminum foil for 10 seconds.
- NOTICE:
- Be sure to keep the reflector in place and make sure that there is nothing between the sensor's left half and the reflector.
- HINT:
- When the reset is completed, the buzzer sounds for 10 seconds.
Disconnect the intelligent tester from the DLC3.
Recheck and readjust the vertical direction of the radar sensor.
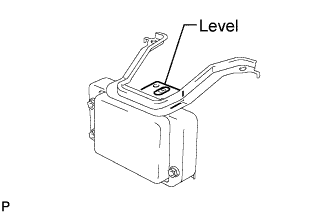
Set a level on the radar sensor's level rack.
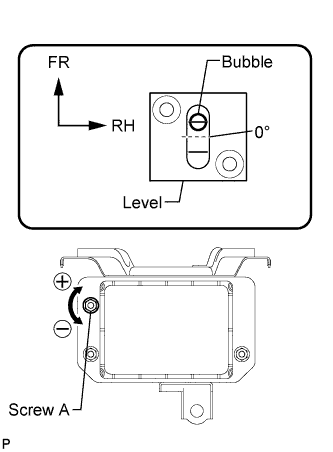
Check that the air bubble is within the red frame on the level.
- OK:
- The air bubble is within the red frame on the level.
- If the bubble is not within the red frame, use a hexagon wrench to adjust screw A until the air bubble is within the red frame.
- HINT:
- Result:
Adjustment Direction Adjustment Procedure Adjustment Angle Vertical adjustment Upward direction: Turn screw A to negative (-) sideDownward direction: Turn screw A to positive (+) sideApprox. 1.0°per turn
17. VEHICLE PREPARATION FOR FOG LIGHT AIM |
Prepare the vehicle:
18. PREPARATION FOR FOG LIGHT AIMING |
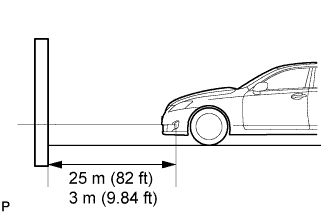
Prepare the vehicle according to the following conditions:
- NOTICE:
- A distance of 25 m (82 ft) between the vehicle (fog light bulb center) and the wall is necessary for proper aim adjustment. If unavailable, secure a distance of exactly 3 m (9.84 ft) for check and adjustment. (The target zone will change with the distance, so follow the instructions in the illustration.)
Prepare a piece of thick white paper (approximately 2 m (6.6 ft) (height) x 4 m (13.1 ft) (width)) to use as a screen.
Draw a vertical line down the center of screen (V line).
Set the screen as shown in the illustration.
- HINT:
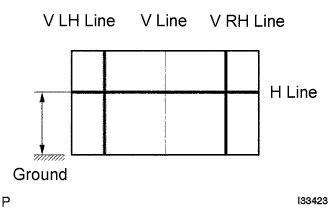
Draw base lines (H line, V LH, V RH lines) on the screen as shown in the illustration.
- HINT:
- Mark the fog light bulb center marks on the screen. If the center mark cannot be observed on the fog light, use the center of the fog light bulb or the manufacturer's name marked on the fog light as the center mark.
H Line (Fog light height):
Draw a horizontal line across the screen so that it passes through the center marks. The H line should be at the same height as the fog light bulb center marks of the low-beam fog lights.
V LH Line, V RH Line (Center mark position of left-hand (LH) and right-hand (RH) fog lights):
Draw two vertical lines so that they intersect the H line at each center mark.
19. FOG LIGHT AIMING INSPECTION |
Cover the fog light or disconnect the connector of the fog light on the opposite side to prevent light from the fog light not being inspected from affecting fog light aiming inspection.
Start the engine.
Turn on the fog light and make sure that the cutoff line falls within the specified area, as shown in the illustration.
20. FOG LIGHT AIMING ADJUSTMENT |
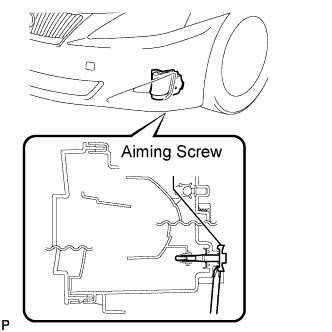
Adjust the fog light aim into the specified range by turning the aiming screw with a screwdriver.
- NOTICE:
- The final turn of the aiming screw should be made in the clockwise direction. If the screw is tightened excessively, loosen it and then retighten it, so that the final turn of the screw is in the clockwise direction.