Cylinder Head Gasket (W/ Dpf) Removal
PRECAUTION
DISCONNECT CABLE FROM NEGATIVE BATTERY TERMINAL
REMOVE NO. 1 TURBOCHARGER SUB-ASSEMBLY WITH EXHAUST MANIFOLD RH AND NO. 2 TURBOCHARGER SUB-ASSEMBLY WITH EXHAUST MANIFOLD LH
CHECK INJECTOR COMPENSATION CODE
REMOVE GENERATOR ASSEMBLY
REMOVE NO. 1 INTAKE AIR CONNECTOR BRACKET
REMOVE AIR TUBE SUPPORT
REMOVE NO. 1 WATER BY-PASS PIPE SUB-ASSEMBLY
REMOVE NO. 4 VACUUM TRANSMITTING PIPE SUB-ASSEMBLY
REMOVE ENGINE MOUNTING BRACKET RH
REMOVE NO. 1 CYLINDER BLOCK INSULATOR
REMOVE NO. 2 INTAKE AIR CONNECTOR BRACKET
REMOVE TURBOCHARGER WIRE
REMOVE NO. 3 VACUUM TRANSMITTING PIPE SUB-ASSEMBLY
REMOVE NO. 2 WATER BY-PASS PIPE SUB-ASSEMBLY
REMOVE ENGINE MOUNTING BRACKET LH
REMOVE NO. 2 CYLINDER BLOCK INSULATOR
REMOVE COMPRESSOR BRACKET
REMOVE STIFFENER INSULATOR RH
DISCONNECT NO. 1 OIL COOLER HOSE
DISCONNECT NO. 2 OIL COOLER HOSE
REMOVE CRANKSHAFT PULLEY
REMOVE TIMING GEAR COVER SPACER
REMOVE OIL FILTER ELEMENT
REMOVE OIL FILTER BRACKET SUB-ASSEMBLY
REMOVE ENGINE OIL LEVEL SENSOR
REMOVE NO. 2 OIL PAN SUB-ASSEMBLY
REMOVE OIL STRAINER SUB-ASSEMBLY
REMOVE NO. 1 OIL PAN SUB-ASSEMBLY
REMOVE CAMSHAFT POSITION SENSOR
REMOVE CRANKSHAFT POSITION SENSOR
REMOVE VISCOUS HEATER ASSEMBLY WITH MAGNET CLUTCH (w/ Viscous Heater)
REMOVE NO. 1 IDLER PULLEY BRACKET (w/ Viscous Heater)
REMOVE WATER INLET
REMOVE THERMOSTAT
REMOVE TIMING GEAR COVER INSULATOR
REMOVE FAN BRACKET SUB-ASSEMBLY
REMOVE NO. 2 IDLER PULLEY (w/ Viscous Heater)
REMOVE NO. 2 IDLER PULLEY BRACKET (w/ Viscous Heater)
REMOVE V-RIBBED BELT TENSIONER ASSEMBLY
DISCONNECT INLET WATER HOSE
REMOVE STARTER ASSEMBLY
REMOVE STARTER HOSE BRACKET
REMOVE NO. 2 INTERCOOLER SUPPORT BRACKET
REMOVE WATER OUTLET
REMOVE WATER OUTLET PIPE
REMOVE NO. 1 GLOW PLUG CONNECTOR
REMOVE GLOW PLUG ASSEMBLY
REMOVE VACUUM PUMP ASSEMBLY
REMOVE CYLINDER HEAD COVER INSULATOR RH
REMOVE FUEL INJECTOR RH
REMOVE CYLINDER HEAD COVER SUB-ASSEMBLY RH
REMOVE NO. 2 FUEL PUMP BRACKET
REMOVE CYLINDER HEAD COVER INSULATOR LH
REMOVE FUEL INJECTOR LH
REMOVE OIL SEPARATOR ASSEMBLY
REMOVE CYLINDER HEAD COVER SUB-ASSEMBLY LH
REMOVE EXHAUST FUEL ADDITION INJECTOR ASSEMBLY
REMOVE FUEL INJECTOR SEAL
REMOVE WATER PUMP ASSEMBLY
REMOVE TIMING CHAIN COVER SUB-ASSEMBLY
REMOVE FRONT CRANKSHAFT OIL SEAL
SET NO. 1 CYLINDER TO TDC/COMPRESSION
REMOVE NO. 1 CRANKSHAFT POSITION SENSOR PLATE
REMOVE PUMP DRIVE SHAFT GEAR
REMOVE NO. 1 CHAIN TENSIONER ASSEMBLY
REMOVE NO. 1 CHAIN TENSIONER SLIPPER
REMOVE NO. 1 CHAIN VIBRATION DAMPER
REMOVE NO. 1 CAMSHAFT TIMING SPROCKET AND NO. 1 TIMING CHAIN
REMOVE NO. 2 CHAIN TENSIONER ASSEMBLY
REMOVE NO. 2 CHAIN TENSIONER SLIPPER
REMOVE NO. 2 CHAIN VIBRATION DAMPER
REMOVE NO. 2 CAMSHAFT TIMING SPROCKET AND NO. 2 TIMING CHAIN
REMOVE FUEL SUPPLY PUMP DRIVE GEAR NUT
REMOVE IDLE GEAR ASSEMBLY
REMOVE NO. 1 IDLE GEAR SHAFT
REMOVE FUEL SUPPLY PUMP DRIVE GEAR
REMOVE FUEL PUMP MOTOR WIRE
REMOVE FUEL SUPPLY PUMP ASSEMBLY
REMOVE V-BANK SILENCER
REMOVE TIMING GEAR CASE SUB-ASSEMBLY
REMOVE NO. 1 AND NO. 2 CAMSHAFTS
REMOVE NO. 3 AND NO. 4 CAMSHAFTS
REMOVE NO. 2 CAMSHAFT BEARING CAP
REMOVE NO. 5 CAMSHAFT BEARING CAP
REMOVE NO. 1 VALVE ROCKER ARM
REMOVE NO. 2 VALVE ROCKER ARM
REMOVE NO. 1 VALVE LASH ADJUSTER ASSEMBLY
REMOVE NO. 2 VALVE LASH ADJUSTER ASSEMBLY
REMOVE CYLINDER HEAD SUB-ASSEMBLY RH
REMOVE CYLINDER HEAD SUB-ASSEMBLY LH
REMOVE NO. 1 CYLINDER HEAD GASKET
REMOVE NO. 2 CYLINDER HEAD GASKET
Cylinder Head Gasket (W/ Dpf) -- Removal |
- CAUTION:
- When replacing an injector (including interchanging injectors between cylinders), common rail, cylinder head, or intake manifold, replace the corresponding injection pipes with a new one.
- NOTICE:
- When fuel lines are disconnected, air may enter the fuel lines, leading to engine starting trouble. Therefore, perform forced regeneration and bleed the air from the fuel lines.
- NOTICE:
- After turning the ignition switch off, waiting time may be required before disconnecting the cable from the battery terminal. Therefore, make sure to read the disconnecting the cable from the battery terminal notice before proceeding with work (Click here).
2. DISCONNECT CABLE FROM NEGATIVE BATTERY TERMINAL |
- NOTICE:
- When disconnecting the cable some systems need to be initialized after the cable is reconnected (Click here).
3. REMOVE NO. 1 TURBOCHARGER SUB-ASSEMBLY WITH EXHAUST MANIFOLD RH AND NO. 2 TURBOCHARGER SUB-ASSEMBLY WITH EXHAUST MANIFOLD LH |
(Click here)
4. CHECK INJECTOR COMPENSATION CODE |
- NOTICE:
- When an injector assembly is replaced, the new injector compensation code must be input into the ECM. When the ECM is replaced, all of the existing injector compensation codes must be input into the new ECM.
- Injector compensation codes are unique, 30-digit, alphanumeric values printed on the head portion of each injector assembly. If an incorrect injector compensation code is input into the ECM, the engine assembly may rattle or engine idling may become rough. In addition, engine failure may occur and the life of the engine may be shortened.
- When an injector compensation code is input into the ECM, the pilot quantity learning values stored in the ECM are initialized. Also, DTC P062F is stored when the pilot quantity learning values are initialized.
Text in Illustration*1
| Injector Compensation Code
|
*a
| Example
|
After replacing injector assemblies with new one(s), input injector compensation code(s) of the injector assemblies into the ECM as follows:
- HINT:
- Each injector assembly has different fuel injection characteristics. In order to optimize the fuel injections, the ECM uses the compensation codes to balance the different fuel injections between each injector assembly.
- When only one or more injector assemblies are replaced, input the injector compensation code(s), perform pilot quantity learning, and then clear the DTCs.
- When the engine switch is turned on (IG) after replacing the ECM, DTC P062F is stored. This indicates that the injector compensation code(s) need to be registered. Manually clear the DTC upon completion of pilot quantity learning.
Input the compensation code(s), which is/are imprinted on the head portion(s) of the new injector assemblies, into the GTS.
Input the new injector compensation code(s) into the ECM using the GTS.
Turn the GTS off and turn the engine switch off.
Wait for at least 30 seconds.
Turn the engine switch on (IG) and turn the GTS on.
Perform pilot quantity learning.
Clear DTC P062F stored in the ECM using the GTS (Click here).
- NOTICE:
- If the DTCs are cleared without performing pilot quantity learning, DTC P062F is stored immediately after clearing DTCs.
Register compensation codes.

Connect the GTS to the DLC3.
Turn the engine switch on (IG).
- NOTICE:
- Do not start the engine.
Turn the GTS on.
Enter the following menus: Engine and ECT / Utility / Injector Compensation.
Press Next.
Press Next again to proceed.
Select "Set Compensation Code".
Press Next.
Select the number of the cylinder corresponding to the injector compensation code that you want to register.
Press Next.
Register compensation code.
- Press Input.
- Manually input the cylinder compensation code using the keyboard on the GTS screen. The code is a 30-digit, alphanumeric value printed on the injector head portion.
- HINT:
- Each injector compensation code is unique. The compensation code for each selected cylinder must be input into the GTS correctly.
- Confirm that the compensation code for the selected cylinder is correct, and then press OK.
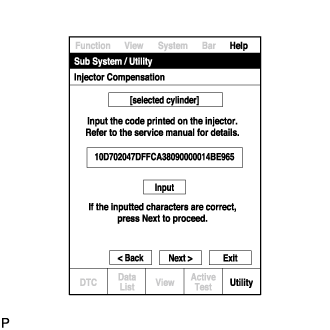
|
Check that the compensation code displayed on the screen is correct by comparing it with the 30-digit alphanumeric value on the head portion of the injector assembly.
- NOTICE:
- If an incorrect injector compensation code is input into the ECM, the engine may rattle or engine idling may become rough. In addition, engine failure may occur and the life of the engine may be shortened.
- HINT:
- If a wrong compensation code is input or read, return to the Input Value screen by pressing Input.
- The saving process may fail due to a problem with the wire harness or a bad connection with the DLC3. Check the wire harness and DLC3 connection. If no problem is found with either, the ECM may be malfunctioning. Check the ECM and repeat this operation.
Press Next to register the injector compensation code in the ECM.
- HINT:
- If the registration process fails, the injector compensation code may be incorrect. Check the injector compensation code again.
- If the input injector compensation code fails to register even though it is input correctly, there may be a problem with the wire harness or a bad connection with the DLC3. Check the wire harness and DLC3 connection. If no problem is found with either, the ECM may be malfunctioning. Check the ECM and restart this operation.
If you want to continue with other compensation code registrations, press Next. To finish the registration, press Exit.
Turn the GTS off and turn the engine switch off.
Wait for at least 30 seconds.
Turn the engine switch on (IG), and then turn the GTS on.
Perform pilot quantity learning.
Clear DTC P062F stored in the ECM using the GTS (Click here).
- NOTICE:
- If the DTCs are cleared without performing pilot quantity learning, DTC P062F is stored immediately after clearing DTCs.
5. REMOVE GENERATOR ASSEMBLY |
Remove the nut and bolt, and disconnect the generator positive (+) cable.
Remove the 3 bolts, 2 nuts and generator.
6. REMOVE NO. 1 INTAKE AIR CONNECTOR BRACKET |
Remove the 2 bolts and No. 1 intake air connector bracket.
7. REMOVE AIR TUBE SUPPORT |
Remove the 2 bolts and air tube support.
8. REMOVE NO. 1 WATER BY-PASS PIPE SUB-ASSEMBLY |
Remove the union bolt, bolt, No. 1 water by-pass pipe and gasket.
9. REMOVE NO. 4 VACUUM TRANSMITTING PIPE SUB-ASSEMBLY |
Disconnect the vacuum hose.
Remove the 2 bolts and No. 4 vacuum transmitting pipe.
10. REMOVE ENGINE MOUNTING BRACKET RH |
Remove the 4 bolts and engine mounting bracket RH.
11. REMOVE NO. 1 CYLINDER BLOCK INSULATOR |
12. REMOVE NO. 2 INTAKE AIR CONNECTOR BRACKET |
Detach the 2 wire harness clamps.
Remove the bolt and No. 2 intake air connector bracket.
13. REMOVE TURBOCHARGER WIRE |
Detach the 3 wire harness clamps.
Remove the 2 bolts and turbocharger wire.
14. REMOVE NO. 3 VACUUM TRANSMITTING PIPE SUB-ASSEMBLY |
w/ Intercooler:
Disconnect the vacuum hose.
Remove the 2 bolts and No. 3 vacuum transmitting pipe.
15. REMOVE NO. 2 WATER BY-PASS PIPE SUB-ASSEMBLY |
Remove the union bolt, 2 bolts, No. 2 water by-pass pipe and gasket.
16. REMOVE ENGINE MOUNTING BRACKET LH |
Remove the 4 bolts and engine mounting bracket LH.
17. REMOVE NO. 2 CYLINDER BLOCK INSULATOR |
18. REMOVE COMPRESSOR BRACKET |
Remove the bolt and compressor bracket.
19. REMOVE STIFFENER INSULATOR RH |
Remove the 2 bolts and stiffener insulator RH.
20. DISCONNECT NO. 1 OIL COOLER HOSE |
Text in Illustration*1
| No. 1 Oil Cooler Hose
|
*2
| No. 2 Oil Cooler Hose
|
21. DISCONNECT NO. 2 OIL COOLER HOSE |
22. REMOVE CRANKSHAFT PULLEY |
- NOTICE:
- This procedure is intended for removal/installation of the crankshaft pulley only. Do not use this procedure for removal/installation of the flywheel or the drive plate and ring gear.
Text in Illustration*1
| Service Hole
|
*2
| Protrusion
|
Install the 2 bolts to the bolt holes of the crankshaft rear side.
Using a bar, turn the crankshaft until the crankshaft pulley service hole is a little to the left of bottom dead center.
Install a 14 mm x 1.5 pitch service bolt with a length of 70 mm or more to the crankshaft pulley service hole, and hold the crankshaft using the timing chain cover protrusion.
Remove the 3 bolts and crankshaft pulley.
- NOTICE:
- If the crankshaft pulley cannot be removed, temporarily install a bolt to the crankshaft so that the pulley does not fall, and lightly tap the outer edge of the mass damper with a plastic-faced hammer to remove the pulley. Do not tap the pulley V-ribbed belt ribs, as the crankshaft may be damaged.
23. REMOVE TIMING GEAR COVER SPACER |
Remove the 2 bolts and timing gear cover spacer.
24. REMOVE OIL FILTER ELEMENT |
Remove the oil filter drain plug.
Connect a hose with an inside diameter of 15 mm (0.591 in.) to the pipe.
Remove the O-ring from the oil filter drain plug and install it to the drain pipe.
Install the oil filter drain pipe to the oil filter cap and drain the engine oil.
Remove the oil filter drain pipe.
Apply a light coat of engine oil to a new O-ring, and install it to the oil filter drain plug.
Install the oil filter drain plug to the oil filter cap.
- Torque:
- 13 N*m{127 kgf*cm, 9 ft.*lbf}
Using SST, remove the oil filter cap.
- SST
- 09228-06501
- HINT:
- Use a container to catch the draining oil. After the oil filter cap is loosened approximately 4 turns and the cap ribs are vertical, engine oil drains from the gap between the oil filter cap and oil pan.
Remove the oil filter element and O-ring from the oil filter cap.
- NOTICE:
- Be sure to remove the cap O-ring by hand, without using any tools, to prevent damage to the cap O-ring groove.
25. REMOVE OIL FILTER BRACKET SUB-ASSEMBLY |
Disconnect the 2 wire harness clamps.
Remove the 3 bolts, 2 nuts and oil filter bracket.
Remove the 2 O-rings.
26. REMOVE ENGINE OIL LEVEL SENSOR |
Disconnect the sensor connector.
Remove the 4 bolts and sensor.
Remove the gasket from the sensor.
27. REMOVE NO. 2 OIL PAN SUB-ASSEMBLY |
Remove the 10 bolts and 2 nuts.
Insert the blade of an oil pan seal cutter between the oil pans. Cut through the applied sealer and remove the No. 2 oil pan.
- NOTICE:
- Be careful not to damage the contact surfaces of the No. 1 and No. 2 oil pans.
28. REMOVE OIL STRAINER SUB-ASSEMBLY |
Remove the 2 bolts and oil strainer.
Remove the O-ring from the oil strainer.
29. REMOVE NO. 1 OIL PAN SUB-ASSEMBLY |
Remove the 20 bolts, 2 nuts and oil reflector plate.
- NOTICE:
- If the oil reflector plate is deformed, replace it.
- HINT:
- Be sure to clean the bolts and stud bolts, and check the threads for cracks or other damage.
Remove the No. 1 oil pan by prying between the No. 1 oil pan and cylinder block with a screwdriver.
- NOTICE:
- Be careful not to damage the contact surfaces of the cylinder block and oil pan.
- HINT:
- Tape the screwdriver tip before use.
Remove the 3 O-rings.
Remove the cylinder block oil hole gasket.
30. REMOVE CAMSHAFT POSITION SENSOR |
Disconnect the sensor connector.
Remove the bolt and sensor.
31. REMOVE CRANKSHAFT POSITION SENSOR |
Disconnect the sensor wire harness clamp.
Remove the bolt and sensor.
32. REMOVE VISCOUS HEATER ASSEMBLY WITH MAGNET CLUTCH (w/ Viscous Heater) |
Disconnect the connector and detach the clamp.
Using pliers, grip the claws of the clips and slide the 2 clips.
Disconnect the 2 heater hoses.
Remove the 2 bolts and heater assembly.
33. REMOVE NO. 1 IDLER PULLEY BRACKET (w/ Viscous Heater) |
Remove the bolt, cover, No. 1 idler pulley and collar.
Disconnect the No. 2 oil cooler hose from the water pump and clamp.
Remove the 4 bolts and water inlet.
Remove the thermostat.
Remove the gasket from the thermostat.
36. REMOVE TIMING GEAR COVER INSULATOR |
w/o Viscous Heater:
Remove the 2 bolts and timing gear cover insulator.
w/ Viscous Heater:
Remove the timing gear cover insulator.
37. REMOVE FAN BRACKET SUB-ASSEMBLY |
Remove the 4 bolts and fan bracket.
38. REMOVE NO. 2 IDLER PULLEY (w/ Viscous Heater) |
Remove the bolt, cover, No. 2 idler pulley and collar.
39. REMOVE NO. 2 IDLER PULLEY BRACKET (w/ Viscous Heater) |
Remove the 3 bolts and idler pulley bracket.
40. REMOVE V-RIBBED BELT TENSIONER ASSEMBLY |
Remove the 3 bolts and V-ribbed belt tensioner bracket.
Remove the bolt and No. 1 idler pulley.
Remove the 5 bolts and V-ribbed belt tensioner.
41. DISCONNECT INLET WATER HOSE |
42. REMOVE STARTER ASSEMBLY |
Detach the harness clamp and disconnect the wire harness.
Disconnect the starter connector.
Remove the nut and disconnect the starter wire.
Disconnect the 2 starter hoses.
Remove the 2 bolts and starter.
43. REMOVE STARTER HOSE BRACKET |
Remove the 2 bolts and starter hose bracket.
44. REMOVE NO. 2 INTERCOOLER SUPPORT BRACKET |
Remove the 2 bolts and No. 2 intercooler support bracket.
Disconnect the engine coolant temperature sensor connector.
Remove the 2 bolts, disconnect the water outlet from the No. 2 water hose joint, and remove the water outlet and gasket.
46. REMOVE WATER OUTLET PIPE |
Remove the 4 bolts, water outlet pipe and 2 gaskets.
47. REMOVE NO. 1 GLOW PLUG CONNECTOR |
Remove the 2 screw grommets and 2 nuts, and disconnect the 2 wire harnesses.
Remove the 8 screw grommets, 8 nuts and 2 glow plug connectors.
Text in Illustration*a
| RH
|
*b
| LH
|
48. REMOVE GLOW PLUG ASSEMBLY |
Using a 10 mm deep socket wrench, remove the 8 glow plugs.
Text in Illustration*a
| RH
|
*b
| LH
|
- HINT:
- Before removing the glow plugs, thoroughly clean off all dirt, sand, etc.
49. REMOVE VACUUM PUMP ASSEMBLY |
Remove the 3 bolts and vacuum pump.
Remove the 2 O-rings.
50. REMOVE CYLINDER HEAD COVER INSULATOR RH |
51. REMOVE FUEL INJECTOR RH |
Remove the 4 bolts, 4 washers, 4 nozzle holder clamps and 4 injectors.
- HINT:
- Arrange the injectors, holder clamps, washers and bolts in the correct order.
Remove the O-ring from each injector.
Remove the 4 injection nozzle seats from the cylinder head.
52. REMOVE CYLINDER HEAD COVER SUB-ASSEMBLY RH |
Remove the 19 bolts, 4 nozzle holder clamp seats and cylinder head cover RH.
Text in Illustration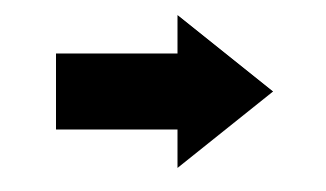
| Bolt
|

| Nozzle Holder Clamp Seat
|
Remove the cylinder head cover gasket RH and No. 3 cylinder head cover gasket from the cylinder head cover RH.
53. REMOVE NO. 2 FUEL PUMP BRACKET |
Remove the bolt and No. 2 fuel pump bracket.
54. REMOVE CYLINDER HEAD COVER INSULATOR LH |
55. REMOVE FUEL INJECTOR LH |
Remove the 4 bolts, 4 washers, 4 nozzle holder clamps and 4 injectors.
- HINT:
- Arrange the injectors, holder clamps, washers and bolts in the correct order.
Remove the O-ring from each injector.
Remove the 4 injection nozzle seats from the cylinder head.
56. REMOVE OIL SEPARATOR ASSEMBLY |
Remove the 3 bolts, oil separator and gasket.
57. REMOVE CYLINDER HEAD COVER SUB-ASSEMBLY LH |
Remove the 18 bolts, 4 nozzle holder clamp seats and cylinder head cover LH.
Text in Illustration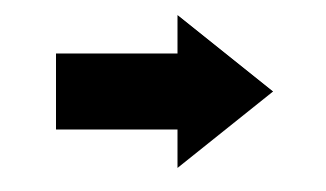
| Bolt
|

| Nozzle Holder Clamp Seat
|
Remove the cylinder head cover gasket LH and No. 4 cylinder head cover gasket from the cylinder head cover LH.
58. REMOVE EXHAUST FUEL ADDITION INJECTOR ASSEMBLY |
Disconnect the 2 exhaust fuel addition injector connectors.
Text in Illustration*A
| for Bank 1
|
*B
| for Bank 2
|
Remove the 2 bolts, 2 washers and 2 nozzle holder clamps.
Text in Illustration*A
| for Bank 1
|
*B
| for Bank 2
|
*1
| Washer
|
*2
| Nozzle Holder Clamp
|
Remove the 2 exhaust fuel addition injectors and 2 gaskets.
59. REMOVE FUEL INJECTOR SEAL |
Remove the 2 fuel injector seals.
Text in Illustration*1
| Fuel Injector Seal
|
60. REMOVE WATER PUMP ASSEMBLY |
Remove the 9 bolts, 2 nuts, water pump and gasket.
61. REMOVE TIMING CHAIN COVER SUB-ASSEMBLY |
Remove the 4 nuts and 16 bolts.
Text in Illustration*1
| Nut
|
Using a screwdriver, remove the timing chain cover by prying between the timing chain cover and timing gear case.
- HINT:
- Tape the screwdriver tip before use.
Remove the O-ring from the timing gear case.
62. REMOVE FRONT CRANKSHAFT OIL SEAL |
Place the timing chain cover on wooden blocks.
Text in Illustration*1
| Wooden Block
|
Using a screwdriver and wooden block, pry out the oil seal.
- NOTICE:
- Do not damage the surface of the oil seal press fit hole.
- HINT:
- Tape the screwdriver tip before use.
63. SET NO. 1 CYLINDER TO TDC/COMPRESSION |
Temporarily install the 2 crankshaft pulley set bolts to the crankshaft.
Turn the crankshaft clockwise to set the No. 1 cylinder to TDC.
With the crankshaft key 45° counterclockwise from the top position, check that the timing marks of the RH and LH camshaft timing gears are aligned. If not as specified, turn the crankshaft 1 revolution (360°) and align the timing marks as shown below.
Text in Illustration*1
| Key
| -
| -
|
*a
| Top
| -
| -
|
Remove the 2 crankshaft pulley set bolts.
64. REMOVE NO. 1 CRANKSHAFT POSITION SENSOR PLATE |
Using a T30 "TORX" wrench, remove the 2 screws and crankshaft position sensor plate.
65. REMOVE PUMP DRIVE SHAFT GEAR |
Using SST, hold the pump drive shaft gear.
- SST
- 09960-10010(09962-01000,09963-01000)
Remove the 4 bolts and pump drive shaft gear.
66. REMOVE NO. 1 CHAIN TENSIONER ASSEMBLY |
Push the tensioner slipper away from the tensioner, and move the stopper plate clockwise to release the lock as shown in A.
Push down the tensioner slipper and move the stopper plate counterclockwise to set the lock as shown in B.
Push the tensioner slipper away from the tensioner, and insert a hexagon wrench into the stopper plate hole as shown in C.
Text in Illustration*1
| Stopper Plate
| -
| -
|
Remove the 2 bolts and No. 1 chain tensioner.
67. REMOVE NO. 1 CHAIN TENSIONER SLIPPER |
68. REMOVE NO. 1 CHAIN VIBRATION DAMPER |
Remove the 2 bolts and No. 1 chain vibration damper.
69. REMOVE NO. 1 CAMSHAFT TIMING SPROCKET AND NO. 1 TIMING CHAIN |
70. REMOVE NO. 2 CHAIN TENSIONER ASSEMBLY |
Push the tensioner slipper away from the tensioner, and move the stopper plate clockwise to release the lock as shown in A.
Push up the tensioner slipper and move the stopper plate counterclockwise to set the lock as shown in B.
Push the tensioner slipper away from the tensioner, and insert a hexagon wrench into the stopper plate hole as shown in C.
Text in Illustration*1
| Stopper Plate
| -
| -
|
Remove the 2 bolts and No. 2 chain tensioner.
71. REMOVE NO. 2 CHAIN TENSIONER SLIPPER |
72. REMOVE NO. 2 CHAIN VIBRATION DAMPER |
Remove the 2 bolts and No. 2 chain vibration damper.
73. REMOVE NO. 2 CAMSHAFT TIMING SPROCKET AND NO. 2 TIMING CHAIN |
Using SST, hold the No. 2 camshaft timing sprocket.
- SST
- 09960-10010(09962-01000,09963-01000)
Remove the 4 bolts, No. 2 camshaft timing sprocket and No. 2 timing chain.
74. REMOVE FUEL SUPPLY PUMP DRIVE GEAR NUT |
Using SST, hold the idle gear.
- SST
- 09960-10010(09962-01000,09963-00700)
Remove the nut.
Text in Illustration*A
| w/ Intercooler
| *B
| w/o Intercooler
|
75. REMOVE IDLE GEAR ASSEMBLY |
w/ Intercooler:
Using an 8 mm x 1.25 pitch service bolt with a length of 15 mm or more, fix the idle gear in place.
- Torque:
- 13 N*m{133 kgf*cm, 10 ft.*lbf}
Remove the 2 bolts, idle gear thrust plate and idle gear.
Text in Illustration*A
| w/ Intercooler
|
*B
| w/o Intercooler
|
76. REMOVE NO. 1 IDLE GEAR SHAFT |
77. REMOVE FUEL SUPPLY PUMP DRIVE GEAR |
Using SST, remove the fuel supply pump drive gear.
- SST
- 09950-50013(09951-05010,09952-05010,09953-05020,09954-05031)
78. REMOVE FUEL PUMP MOTOR WIRE |
Disconnect the 2 connectors and remove the bolt and fuel pump motor wire.
79. REMOVE FUEL SUPPLY PUMP ASSEMBLY |
Using a 6 mm hexagon wrench, remove the hexagon bolt. Then remove the 2 nuts and fuel supply pump.
Remove the O-ring.
80. REMOVE V-BANK SILENCER |
81. REMOVE TIMING GEAR CASE SUB-ASSEMBLY |
Remove the 22 bolts, 2 nuts and timing gear case shown in the illustration.
Text in Illustration*1
| Nut
|
Remove the 2 O-rings and timing gear case gasket.
82. REMOVE NO. 1 AND NO. 2 CAMSHAFTS |
Using a 6 mm x 1.0 pitch service bolt with a length of 16 mm or more, fix the No. 1 camshaft in place.
- Torque:
- 8.0 N*m{82 kgf*cm, 71 in.*lbf}
Loosen the 2 union bolts.
Uniformly loosen and remove the 20 bolts in the sequence shown in the illustration.
Remove the 2 union bolts and No. 1 and No. 2 oil feed pipes.
Remove the 8 No. 3 camshaft bearing caps and No. 1 camshaft bearing cap.
- HINT:
- Be sure to arrange the removed parts for each installation position separately.
Remove the No. 1 and No. 2 camshafts.
83. REMOVE NO. 3 AND NO. 4 CAMSHAFTS |
Using a 6 mm x 1.0 pitch service bolt with a length of 16 mm or more, fix the No. 4 camshaft in place.
- Torque:
- 8.0 N*m{82 kgf*cm, 71 in.*lbf}
Loosen the 2 union bolts.
Uniformly loosen and remove the 20 bolts in the sequence shown in the illustration.
Remove the 2 union bolts and No. 3 and No. 4 oil feed pipes.
Remove the 8 No. 3 camshaft bearing caps and No. 4 camshaft bearing cap.
- HINT:
- Be sure to arrange the removed parts for each installation position separately.
Remove the No. 3 and No. 4 camshafts.
84. REMOVE NO. 2 CAMSHAFT BEARING CAP |
85. REMOVE NO. 5 CAMSHAFT BEARING CAP |
86. REMOVE NO. 1 VALVE ROCKER ARM |
Remove the 16 No. 1 valve rocker arms.
- HINT:
- Be sure to arrange the removed parts for each installation position separately.
87. REMOVE NO. 2 VALVE ROCKER ARM |
Remove the 16 No. 2 valve rocker arms.
- HINT:
- Be sure to arrange the removed parts for each installation position separately.
88. REMOVE NO. 1 VALVE LASH ADJUSTER ASSEMBLY |
Remove the 16 No. 1 valve lash adjusters.
- HINT:
- Be sure to arrange the removed parts for each installation position separately.
89. REMOVE NO. 2 VALVE LASH ADJUSTER ASSEMBLY |
Remove the 16 No. 2 valve lash adjusters.
- HINT:
- Be sure to arrange the removed parts for each installation position separately.
90. REMOVE CYLINDER HEAD SUB-ASSEMBLY RH |
Uniformly loosen and remove the 10 bolts and 10 spacers in the sequence shown in the illustration. Then remove the cylinder head.
- NOTICE:
- Be careful not to drop washers into the cylinder head.
- Head warpage or cracking could result from removing bolts in an incorrect order.
- HINT:
- Be sure to arrange the removed parts for each installation position separately.
91. REMOVE CYLINDER HEAD SUB-ASSEMBLY LH |
Uniformly loosen and remove the 10 bolts and 10 spacers in the sequence shown in the illustration. Then remove the cylinder head.
- NOTICE:
- Be careful not to drop washers into the cylinder head.
- Head warpage or cracking could result from removing bolts in an incorrect order.
- HINT:
- Be sure to arrange the removed parts for each installation position separately.
92. REMOVE NO. 1 CYLINDER HEAD GASKET |
93. REMOVE NO. 2 CYLINDER HEAD GASKET |