INSTALL NO. 2 CAMSHAFT TIMING SPROCKET AND NO. 2 TIMING CHAIN
INSTALL NO. 1 CAMSHAFT TIMING SPROCKET AND NO. 1 TIMING CHAIN
INSTALL VISCOUS HEATER ASSEMBLY WITH MAGNET CLUTCH (w/ Viscous Heater)
Cylinder Head Gasket (W/ Dpf) -- Installation |
- NOTICE:
- Before performing these installation procedures, sufficiently clean and remove any foreign matter from the cylinder block, cylinder head, camshaft and other parts.
- When replacing an injector (including interchanging injectors between cylinders), common rail, cylinder head, or intake manifold, replace the corresponding injection pipes with a new one.
- When fuel lines are disconnected, air may enter the fuel lines, leading to engine starting trouble. Therefore, perform forced regeneration and bleed the air from the fuel lines (Click here).
1. CHECK INJECTOR COMPENSATION CODE |
![]() |
- NOTICE:
- When an injector assembly is replaced, the new injector compensation code must be input into the ECM. When the ECM is replaced, all of the existing injector compensation codes must be input into the new ECM.
- Injector compensation codes are unique, 30-digit, alphanumeric values printed on the head portion of each injector assembly. If an incorrect injector compensation code is input into the ECM, the engine assembly may rattle or engine idling may become rough. In addition, engine failure may occur and the life of the engine may be shortened.
- When an injector compensation code is input into the ECM, the pilot quantity learning values stored in the ECM are initialized. Also, DTC P062F is stored when the pilot quantity learning values are initialized.
*1 | Injector Compensation Code |
*a | Example |
After replacing injector assemblies with new one(s), input injector compensation code(s) of the injector assemblies into the ECM as follows:
- HINT:
- Each injector assembly has different fuel injection characteristics. In order to optimize the fuel injections, the ECM uses the compensation codes to balance the different fuel injections between each injector assembly.
- When only one or more injector assemblies are replaced, input the injector compensation code(s), perform pilot quantity learning, and then clear the DTCs.
- When the engine switch is turned on (IG) after replacing the ECM, DTC P062F is stored. This indicates that the injector compensation code(s) need to be registered. Manually clear the DTC upon completion of pilot quantity learning.
Input the compensation code(s), which is/are imprinted on the head portion(s) of the new injector assemblies, into the GTS.
Input the new injector compensation code(s) into the ECM using the GTS.
Turn the GTS off and turn the engine switch off.
Wait for at least 30 seconds.
Turn the engine switch on (IG) and turn the GTS on.
Perform pilot quantity learning.
Clear DTC P062F stored in the ECM using the GTS (Click here).
- NOTICE:
- If the DTCs are cleared without performing pilot quantity learning, DTC P062F is stored immediately after clearing DTCs.
Register compensation codes.
Connect the GTS to the DLC3.
Turn the engine switch on (IG).
- NOTICE:
- Do not start the engine.
Turn the GTS on.
Enter the following menus: Engine and ECT / Utility / Injector Compensation.
Press Next.
Press Next again to proceed.
Select "Set Compensation Code".
Press Next.
Select the number of the cylinder corresponding to the injector compensation code that you want to register.
Press Next.
Register compensation code.
- Press Input.
Manually input the cylinder compensation code using the keyboard on the GTS screen. The code is a 30-digit, alphanumeric value printed on the injector head portion.- HINT:
- Each injector compensation code is unique. The compensation code for each selected cylinder must be input into the GTS correctly.
- Confirm that the compensation code for the selected cylinder is correct, and then press OK.
- Press Input.
Check that the compensation code displayed on the screen is correct by comparing it with the 30-digit alphanumeric value on the head portion of the injector assembly.
- NOTICE:
- If an incorrect injector compensation code is input into the ECM, the engine may rattle or engine idling may become rough. In addition, engine failure may occur and the life of the engine may be shortened.
- HINT:
- If a wrong compensation code is input or read, return to the Input Value screen by pressing Input.
- The saving process may fail due to a problem with the wire harness or a bad connection with the DLC3. Check the wire harness and DLC3 connection. If no problem is found with either, the ECM may be malfunctioning. Check the ECM and repeat this operation.
Press Next to register the injector compensation code in the ECM.
- HINT:
- If the registration process fails, the injector compensation code may be incorrect. Check the injector compensation code again.
- If the input injector compensation code fails to register even though it is input correctly, there may be a problem with the wire harness or a bad connection with the DLC3. Check the wire harness and DLC3 connection. If no problem is found with either, the ECM may be malfunctioning. Check the ECM and restart this operation.
If you want to continue with other compensation code registrations, press Next. To finish the registration, press Exit.
Turn the GTS off and turn the engine switch off.
Wait for at least 30 seconds.
Turn the engine switch on (IG), and then turn the GTS on.
Perform pilot quantity learning.
Clear DTC P062F stored in the ECM using the GTS (Click here).
- NOTICE:
- If the DTCs are cleared without performing pilot quantity learning, DTC P062F is stored immediately after clearing DTCs.
2. SELECT CYLINDER HEAD GASKET |
Set the 2 crankshaft pulley set bolts to the crankshaft.
Clean the cylinder block with solvent.
Inspect the protrusion for each cylinder.
Set the piston of the cylinder to be measured to slightly before TDC.
Place a dial indicator on the cylinder block, and set the measuring tip as shown in the illustration.
- NOTICE:
- Make sure that the dial indicator is at a right angle to the cylinder block top surface.
Set the dial indicator at 0 mm (0 in.).
- HINT:
- Make sure that the measuring tip is flat against the cylinder block surface and piston head when taking the measurements.
Find where the piston head protrudes most by slowly turning the crankshaft clockwise and counterclockwise.
Measure the piston protrusion value of each cylinder at 2 places as shown in the illustration below, making a total of 8 measurements.
- Standard piston protrusion:
- 0.520 to 0.780 mm (0.0205 to 0.0307 in.)
Text in Illustration *A for Bank 1 *B for Bank 2 *a Measuring Point - - Front - -
Select a new cylinder head gasket.
Text in Illustration *A for Bank 1 *B for Bank 2 Front - - - HINT:
- Cylinder head gaskets are marked A, B, C, D or E accordingly.
- New Installed Cylinder Head Gasket Thickness:
Item Cutout Specified Condition* A 1 1.20 to 1.30 mm (0.0472 to 0.0512 in.) B 2 1.25 to 1.35 mm (0.0492 to 0.0394 in.) C 3 1.30 to 1.40 mm (0.0512 to 0.0551 in.) D 4 1.35 to 1.45 mm (0.0531 to 0.0571 in.) E 5 1.40 to 1.50 mm (0.0551 to 0.0591 in.)
- HINT:
- *: The specified condition indicates the thickness of the gasket after tightening the cylinder head.
Select the largest piston protrusion value from the measurements and then select a new appropriate gasket according to the table below.
- Standard Piston Protrusion:
Item Specified Condition A 0.520 to 0.575 mm (0.0205 to 0.0226 in.) B 0.575 to 0.625 mm (0.0226 to 0.0246 in.) C 0.625 to 0.675 mm (0.0246 to 0.0266 in.) D 0.675 to 0.725 mm (0.0266 to 0.0285 in.) E 0.725 to 0.780 mm (0.0285 to 0.0307 in.)
3. INSTALL NO. 2 CYLINDER HEAD GASKET |
Remove any oil from the contact surface.
Text in Illustration *a Front *b Exhaust Side
![]() |
Place the cylinder head gasket on the cylinder block surface with the front face of the indicated mark "L" upward and facing the exhaust side.
4. INSTALL NO. 1 CYLINDER HEAD GASKET |
Remove any oil from the contact surface.
Text in Illustration *a Front *b Exhaust Side
![]() |
Place the cylinder head gasket on the cylinder block surface with the front face of the indicated mark "R" upward and facing the exhaust side.
5. INSTALL CYLINDER HEAD SUB-ASSEMBLY LH |
Place the cylinder head on the cylinder head gasket.
- NOTICE:
- Ensure that no oil is on the mounting surface of the cylinder head.
Inspect the cylinder head bolts (Click here).
Apply a light coat of engine oil to the threads and under the heads of the cylinder head bolts.
Step 1:
Install and uniformly tighten the 10 cylinder head bolts with the spacers in several steps, in the sequence shown in the illustration.
- Torque:
- 80 N*m{816 kgf*cm, 59 ft.*lbf}
- HINT:
- The cylinder head bolts are tightened in 4 progressive steps.
- If a cylinder head bolt is broken or deformed, replace it.
Step 2:
Mark the cylinder head bolt heads with paint as shown in the illustration.
Text in Illustration *1 Painted Mark Front Tighten the cylinder head bolts 90° in the sequence shown in step 1.
![]() |
Step 3:
Tighten the cylinder head bolts another 90° in the sequence shown in step 1.
Text in Illustration *1 Painted Mark Front
![]() |
Step 4:
Tighten the cylinder head bolts by an additional 90° in the sequence shown in step 1.
Text in Illustration *1 Painted Mark Front
![]() |
Check that the painted marks are now facing the exhaust port side.
6. INSTALL CYLINDER HEAD SUB-ASSEMBLY RH |
Place the cylinder head on the cylinder head gasket.
- NOTICE:
- Ensure that no oil is on the mounting surface of the cylinder head.
Inspect the cylinder head bolts (Click here).
Apply a light coat of engine oil to the threads and under the heads of the cylinder head bolts.
Step 1:
Install and uniformly tighten the 10 cylinder head bolts with the spacers in several steps, in the sequence shown in the illustration.
- Torque:
- 80 N*m{816 kgf*cm, 59 ft.*lbf}
- HINT:
- The cylinder head bolts are tightened in 4 progressive steps.
- If a cylinder head bolt is broken or deformed, replace it.
Step 2:
Mark the cylinder head bolt heads with paint as shown in the illustration.
Text in Illustration *1 Painted Mark Front Tighten the cylinder head bolts 90° in the sequence shown in step 1.
![]() |
Step 3:
Tighten the cylinder head bolts another 90° in the sequence shown in step 1.
Text in Illustration *1 Painted Mark Front
![]() |
Step 4:
Tighten the cylinder head bolts by an additional 90° in the sequence shown in step 1.
Text in Illustration *1 Painted Mark Front
![]() |
Check that the painted marks are now facing the intake port side.
7. SET NO. 1 CYLINDER TO 45° BEFORE TDC |
Using a bar, turn the crankshaft counterclockwise until the No. 1 cylinder is at a position 45° before TDC.
- NOTICE:
- Do not turn the crankshaft again until after the timing gear is installed.
- HINT:
- The No. 1 cylinder is at a position 45° before TDC if the crankshaft counterweight is overlapping the cylinder block hole as shown in the illustration.
![]() |
Remove the 2 crankshaft pulley set bolts.
8. INSTALL NO. 2 VALVE LASH ADJUSTER ASSEMBLY |
- NOTICE:
- Be sure to inspect the valve lash adjuster before installing it (Click here).
Install the 16 No. 2 valve lash adjusters to the cylinder head.
- HINT:
- Install the lash adjuster at the same place it was removed from.
9. INSTALL NO. 1 VALVE LASH ADJUSTER ASSEMBLY |
- NOTICE:
- Be sure to inspect the valve lash adjuster before installing it (Click here).
Install the 16 No. 1 valve lash adjusters to the cylinder head.
- HINT:
- Install the lash adjuster at the same place it was removed from.
10. INSTALL NO. 2 VALVE ROCKER ARM |
Apply engine oil to the lash adjuster tips and valve stem ends.
![]() |
Install the 16 No. 2 valve rocker arms as shown in the illustration.
- HINT:
- Install the valve rocker arm at the same place it was removed from.
11. INSTALL NO. 1 VALVE ROCKER ARM |
Apply engine oil to the lash adjuster tips and valve stem ends.
![]() |
Install the 16 No. 1 valve rocker arms as shown in the illustration.
- HINT:
- Install the valve rocker arm at the same place it was removed from.
12. INSTALL NO. 5 CAMSHAFT BEARING CAP |
Align the camshaft bearing cap and the ring pins of the cylinder head, and install the cap.
13. INSTALL NO. 2 CAMSHAFT BEARING CAP |
Align the camshaft bearing cap and the ring pins of the cylinder head, and install the cap.
14. INSTALL NO. 3 AND NO. 4 CAMSHAFTS |
Add more than 19 cc (1.16 cu. in.) of engine oil into the cylinder head side oil holes.
![]() |
Apply engine oil to the rollers of the valve rocker arms and camshaft housing of the cylinder head.
![]() |
Install the camshafts.
Apply engine oil to the camshaft journals, lobes, thrust portion and gears.
Align the timing marks (1 dot mark) on the back side of the No. 3 and No. 4 camshaft timing gears as shown in the illustration.
Place the camshafts into the cylinder head.
- NOTICE:
- Before and after setting the camshafts, firmly set the rocker arms to the lash adjusters.
![]() |
Install the No. 4 camshaft bearing cap.
Align the No. 4 camshaft bearing cap and the ring pins of the No. 5 camshaft bearing cap.
Temporarily install the 4 bolts by hand.
![]() |
Install the No. 3 camshaft bearing caps.
Confirm the marks and numbers on the camshaft bearing caps and place them in their proper position and direction.
Temporarily install the 8 bolts, which are not installed with the oil feed pipe, by hand.
![]() |
Temporarily install the No. 3 and No. 4 camshaft oil feed pipes with the 8 bolts by hand.
- NOTICE:
- If even one of the pipe bolt holes does not match its camshaft bearing cap bolt hole, replace the camshaft oil feed pipe.
- HINT:
- The pipe is bent on the intake side, and straight on the exhaust side.
![]() |
Temporarily install the 2 union bolts by hand.
![]() |
Uniformly tighten the 20 bolts in several steps in the order shown in the illustration.
- Torque:
- for 12 mm head bolt of No. 4 camshaft bearing cap:
- 21 N*m{214 kgf*cm, 15 ft.*lbf}
- for 10 mm head bolt of No. 3 camshaft bearing cap:
- 10 N*m{102 kgf*cm, 7 ft.*lbf}
Text in Illustration *1 12 mm Head Bolt *2 10 mm Head Bolt
![]() |
Tighten the 2 union bolts.
- Torque:
- 17 N*m{173 kgf*cm, 13 ft.*lbf}
![]() |
Remove the service bolt from the No. 4 camshaft timing gear.
- NOTICE:
- Do not drop the bolt into the engine.
![]() |
15. INSTALL NO. 1 AND NO. 2 CAMSHAFT |
Add more than 19 cc (1.16 cu. in.) of engine oil into the cylinder head side oil holes.
![]() |
Apply engine oil to the rollers of the valve rocker arms and the camshaft housing of the cylinder head.
![]() |
Install the camshafts.
Apply engine oil to the camshaft journals, lobes, thrust portion and gears.
Align the timing marks (2 dot marks) on the back side of the No. 1 and No. 2 camshaft timing gears as shown in the illustration.
Place the camshafts into the cylinder head.
- NOTICE:
- Before and after setting the camshafts, firmly set the rocker arms to the lash adjusters.
![]() |
Install the No. 1 camshaft bearing cap.
Align the No. 1 camshaft bearing cap and the ring pins of the No. 2 camshaft bearing cap.
Temporarily install the 4 bolts by hand.
![]() |
Install the No. 3 camshaft bearing caps.
Confirm the marks and numbers on the camshaft bearing caps and place them in their proper position and direction.
Temporarily install the 8 bolts, which are not installed with the oil feed pipe, by hand.
![]() |
Temporarily install the No. 1 and No. 2 camshaft oil feed pipes with the 8 bolts by hand.
- NOTICE:
- If even one of the pipe bolt holes does not match its camshaft bearing cap bolt hole, replace the camshaft oil feed pipe.
- HINT:
- The pipe is bent on the intake side, and straight on the exhaust side.
![]() |
Temporarily install the 2 union bolts by hand.
![]() |
Uniformly tighten the 20 bolts in several steps in the order shown in the illustration.
- Torque:
- for 12 mm head bolt of No. 1 camshaft bearing cap:
- 21 N*m{214 kgf*cm, 15 ft.*lbf}
- for 10 mm head bolt of No. 3 camshaft bearing cap:
- 10 N*m{102 kgf*cm, 7 ft.*lbf}
Text in Illustration *1 12 mm Head Bolt *2 10 mm Head Bolt
![]() |
Tighten the 2 union bolts.
- Torque:
- 17 N*m{173 kgf*cm, 13 ft.*lbf}
![]() |
Remove the service bolt from the No. 1 camshaft timing gear.
- NOTICE:
- Do not drop the bolt into the engine.
![]() |
16. INSTALL TIMING GEAR CASE SUB-ASSEMBLY |
- NOTICE:
- When the contact surfaces shown below are wet, wipe them with an oil-free cloth before applying seal packing.
*a | Cylinder Block | *b | Timing Gear Case |
Apply seal packing to the timing gear case as shown in the following illustration.
- Standard seal diameter:
- 4 to 5 mm (0.157 to 0.197 in.)
- Seal packing:
- Toyota Genuine Seal Packing Black, Three Bond 1207B or equivalent
- NOTICE:
- After applying seal packing, align the timing gear case with the engine within 3 minutes and tighten the bolts and nuts within 15 minutes.
- Apply the seal packing in a continuous line.
- HINT:
- The FIPG line is shown below.
- Apply packing to the 5 seal surface areas.
Text in Illustration *a Seal Diameter: 4 to 5 mm - -
Install a new timing gear case gasket.
Text in Illustration *1 New Timing Gear Case Gasket *2 New O-Ring
![]() |
Apply engine oil to 2 new O-rings and install them to the timing gear case.
Install the timing gear case with the 22 bolts and 2 nuts.
- Torque:
- for 14 mm head bolt (When "dry"):
- 46 N*m{469 kgf*cm, 34 ft.*lbf}
- for 14 mm head bolt (When "wet"):
- 42 N*m{428 kgf*cm, 31 ft.*lbf}
- for 12 mm head bolt A and B:
- 29 N*m{296 kgf*cm, 21 ft.*lbf}
- for nut:
- 29 N*m{296 kgf*cm, 21 ft.*lbf}
Text in Illustration *1 Nut *2 14 mm Head Bolt *3 12 mm Head Bolt A *4 12 mm Head Bolt B - NOTICE:
- The case is "dry" when there is absolutely no engine oil on the 14 mm head bolts and cylinder head bolt holes.
- The case is "wet" when there is engine oil on the 14 mm head bolts and cylinder head bolt holes.
Bolt Length Item Quantity Length A 4 20 mm (0.787 in.) B 8 45 mm (1.77 in.)
![]() |
17. INSTALL V-BANK SILENCER |
Align the alignment areas of the V-bank silencer and cylinder block, and install the V-bank silencer.
- NOTICE:
- Verify that the V-bank silencer is below the top surface of the intake port of the cylinder head RH and LH.
18. INSTALL FUEL SUPPLY PUMP ASSEMBLY |
Using an 8 mm x 1.25 pitch tap, remove the adhesive from the timing gear case side bolt hole.
![]() |
Apply adhesive to 2 or more threads of the timing gear case bolt hole.
- Adhesive:
- Toyota Genuine Adhesive 1344, Three Bond 1344 or equivalent
Text in Illustration *1 Adhesive
![]() |
Apply engine oil to a new O-ring and install it to the supply pump.
Text in Illustration *1 New O-Ring
![]() |
Install the supply pump to the timing gear case.
- NOTICE:
- When installing the supply pump, do not hold the fuel pipe to prevent fuel leaks.
Temporarily install the 2 nuts.
Using a 6 mm hexagon wrench, install the hexagon bolt, and then tighten the 2 nuts.
- Torque:
- 21 N*m{214 kgf*cm, 15 ft.*lbf}
19. INSTALL FUEL PUMP MOTOR WIRE |
Install the fuel pump wire with the bolt.
- Torque:
- 6.0 N*m{61 kgf*cm, 53 in.*lbf}
- HINT:
- Attach the claw of the bracket to the timing gear case when installing the bracket.
![]() |
20. INSPECT RADIAL BALL BEARING |
Turn the bearing, and check that the bearing moves smoothly and quietly.
If it moves roughly or noisily, replace the radial ball bearing.
![]() |
21. TEMPORARILY INSTALL FUEL SUPPLY PUMP DRIVE GEAR |
Align the cutout of the supply pump drive gear and key of the supply pump, and temporarily install the fuel supply pump drive gear nut.
![]() |
22. SET NO. 1 AND NO. 2 CAMSHAFTS TO TDC |
Using a wrench, turn the No. 1 camshaft and align the timing marks (1 dot mark) on the back side of the timing gears as shown in the illustration.
![]() |
23. INSTALL NO. 1 IDLE GEAR SHAFT |
Apply engine oil to the contact surface of the idle gear shaft and the back side of the protrusion.
![]() |
Install the idle gear shaft to the cylinder block.
24. INSTALL IDLE GEAR ASSEMBLY |
Temporarily install the 2 crankshaft pulley set bolts to the crankshaft.
Text in Illustration *1 Key
![]() |
Using a bar, turn the crankshaft clockwise to the No. 1 cylinder TDC position.
Align the timing marks of the supply pump drive gear and idle gear, and the timing marks of the crankshaft timing gear and idle gear as shown in the illustration.
Text in Illustration *A w/ Intercooler *B w/o Intercooler
Apply engine oil to the idle gear thrust plate and gears.
Install the idle gear thrust plate with the 2 bolts.
- Torque:
- 47 N*m{479 kgf*cm, 35 ft.*lbf}
w/ Intercooler:
Remove the service bolt.
25. TIGHTEN FUEL SUPPLY PUMP DRIVE GEAR NUT |
Using SST, hold the idle gear and tighten the nut.
- SST
- 09960-10010(09962-01000,09963-00700)
- Torque:
- 68 N*m{693 kgf*cm, 50 ft.*lbf}
Text in Illustration *A w/ Intercooler *B w/o Intercooler
26. CHECK NO. 1 CYLINDER TO TDC/COMPRESSION |
Check that the timing marks of the following pairs of parts are aligned: 1) supply pump drive gear and idle gear: 2) crankshaft timing gear and idle gear: 3) RH and LH camshaft timing gears.
27. INSTALL NO. 2 CAMSHAFT TIMING SPROCKET AND NO. 2 TIMING CHAIN |
Align the 2 mark plates (yellow) on the No. 2 timing chain with the timing mark (1 dot mark) of the No. 2 camshaft timing sprocket as shown in the illustration.
![]() |
Align the No. 2 timing chain mark plate (yellow) with the supply pump drive gear timing mark, and temporarily install the No. 2 camshaft timing sprocket with the 4 bolts.
Text in Illustration *1 Timing Mark
![]() |
Using SST, hold the No. 2 camshaft timing sprocket, and tighten the 4 bolts.
- SST
- 09960-10010(09962-01000,09963-01000)
- Torque:
- 25 N*m{250 kgf*cm, 18 ft.*lbf}
![]() |
28. INSTALL NO. 1 CAMSHAFT TIMING SPROCKET AND NO. 1 TIMING CHAIN |
Align the 2 mark plates (yellow) on the No. 1 timing chain with the timing mark (1 dot mark) of the No. 1 camshaft timing sprocket as shown in the illustration.
![]() |
Align the No. 1 timing chain mark plate (yellow) with the supply pump drive gear timing mark, and temporarily install the No. 1 camshaft timing sprocket.
Text in Illustration *1 Timing Mark
![]() |
29. INSTALL PUMP DRIVE SHAFT GEAR |
Temporarily install the pump drive shaft gear with the 4 bolts.
![]() |
Using SST, hold the pump drive shaft gear and tighten the 4 bolts.
- SST
- 09960-10010(09962-01000,09963-01000)
- Torque:
- 25 N*m{250 kgf*cm, 18 ft.*lbf}
30. INSTALL NO. 2 CHAIN VIBRATION DAMPER |
Install the No. 2 chain vibration damper with the 2 bolts.
- Torque:
- 21 N*m{214 kgf*cm, 15 ft.*lbf}
31. INSTALL NO. 2 CHAIN TENSIONER SLIPPER |
32. INSTALL NO. 2 CHAIN TENSIONER ASSEMBLY |
Move the stopper plate clockwise to release the lock, and push the plunger into the tensioner.
![]() |
Move the stopper plate counterclockwise to set the lock, and insert a hexagon wrench into the stopper plate hole.
Install the No. 2 chain tensioner with the 2 bolts.
- Torque:
- 10 N*m{102 kgf*cm, 7 ft.*lbf}
Remove the hexagon wrench.
33. INSTALL NO. 1 CHAIN VIBRATION DAMPER |
Install the No. 1 chain vibration damper with the 2 bolts.
- Torque:
- 21 N*m{214 kgf*cm, 15 ft.*lbf}
34. INSTALL NO. 1 CHAIN TENSIONER SLIPPER |
35. INSTALL NO. 1 CHAIN TENSIONER ASSEMBLY |
Move the stopper plate clockwise to release the lock, and push the plunger into the tensioner.
![]() |
Move the stopper plate counterclockwise to set the lock, and insert a hexagon wrench into the stopper plate hole.
Install the No. 1 chain tensioner with the 2 bolts.
- Torque:
- 10 N*m{102 kgf*cm, 7 ft.*lbf}
Remove the hexagon wrench.
36. INSTALL NO. 1 CRANKSHAFT POSITION SENSOR PLATE |
Remove the adhesive from the threads of the 2 screws and the bolt holes of the crankshaft.
Apply adhesive to 2 or 3 threads of the 2 screws.
- Adhesive:
- Toyota Genuine Adhesive 1344, Three Bond 1344 or equivalent
Text in Illustration *1 Adhesive
![]() |
Using a T30 "TORX" wrench, install the No. 1 crankshaft position sensor plate with the 2 screws.
- Torque:
- 10 N*m{102 kgf*cm, 7 ft.*lbf}
- NOTICE:
- Make sure the "F" mark on the plate is facing towards the front side of the engine.
- HINT:
- When replacing the No. 1 crankshaft position sensor plate, perform "Crank Time Compensation Reset" (Click here).
37. CHECK NO. 1 CYLINDER TO TDC/COMPRESSION |
Temporarily install the 2 crankshaft pulley set bolts to the crankshaft.
Rotate the crankshaft 2 revolutions or more so that the crankshaft key is 45° counterclockwise from the top. Check that the timing marks (1 dot mark each) of the RH and LH camshaft timing gears align. If not as specified, turn the crankshaft 1 revolution (360°) and align the timing marks. If the timing marks are deviated, reinstall the chain and camshaft.
Text in Illustration *1 Key - - *a Top - -
Remove the 2 crankshaft pulley set bolts.
38. INSTALL FRONT CRANKSHAFT OIL SEAL |
Place the timing chain cover on wooden blocks.
![]() |
Using SST and a hammer, tap in a new oil seal as shown in the illustration.
- SST
- 09316-12010
09950-70010(09951-07100)
09950-60020(09951-00890)
- Standard depth A:
- 0.6 to 1.4 mm (0.0236 to 0.0551 in.)
39. INSTALL TIMING CHAIN COVER SUB-ASSEMBLY |
- NOTICE:
- When the contact surfaces shown below are wet, wipe them with an oil-free cloth before applying seal packing.
*1 | Timing Gear Case | *2 | Timing Chain Cover |
Install a new O-ring to the timing gear case.
Text in Illustration *1 New O-Ring
![]() |
Apply seal packing to the timing chain cover as shown in the following illustration.
- Standard seal diameter:
- 4 to 5 mm (0.157 to 0.197 in.)
- Seal packing:
- Toyota Genuine Seal Packing Black, Three Bond 1207B or equivalent
- NOTICE:
- After applying seal packing, align the timing chain cover with the timing gear case within 3 minutes and tighten the bolts and nuts within 15 minutes.
- Apply the seal packing in a continuous line.
- Make sure the seal packing does not become thinner than 4 mm (0.157 in.) at the areas labeled "B" in the illustration below.
- HINT:
- The FIPG line is shown below.
- Apply packing to the 6 seal surface areas.
Text in Illustration *a Seal Diameter: 4 to 5 mm - -
Apply engine oil to the lip of the oil seal.
Align and install the timing chain cover to the timing gear case knock pin and supply pump bearing.
- NOTICE:
- Make sure that the lip of the oil seal is properly installed.
If the stud bolts are loose, tighten them using an E7 "TORX" wrench.
- Torque:
- 6.0 N*m{61 kgf*cm, 53 in.*lbf}
Text in Illustration *1 Stud Bolt
![]() |
Install and uniformly tighten the 16 bolts and 4 nuts in the order shown in the illustration.
- Torque:
- 25 N*m{250 kgf*cm, 18 ft.*lbf}
Text in Illustration *1 Nut
![]() |
40. INSTALL FUEL INJECTOR SEAL |
Install 2 new fuel injector seals.
41. INSTALL EXHAUST FUEL ADDITION INJECTOR ASSEMBLY |
- NOTICE:
- If there is foreign matter on the installation surface of the exhaust fuel addition injector, be sure to clean it before installation.
Install 2 new gaskets, the 2 exhaust fuel addition injectors, 2 nozzle holder clamps and 2 new washers with the 2 bolts.
- Torque:
- 28 N*m{286 kgf*cm, 21 ft.*lbf}
- HINT:
- Align the nozzle holder clamp with the cutouts of the injector as shown in the illustration.
Text in Illustration *1 Nozzle Holder Clamp
![]() |
42. TEMPORARILY INSTALL INTAKE MANIFOLD |
Install the gasket and temporarily install the No. 2 intake manifold with the 9 bolts.
![]() |
Install the gasket and temporarily install the No. 1 intake manifold with the 9 bolts.
![]() |
Install the 2 gaskets and temporarily install the No. 3 intake manifold with the 16 bolts.
Bolt Length Item Length Bolt A 25 mm (0.984 in.) Bolt B 70 mm (2.76 in.)
![]() |
43. INSTALL CYLINDER HEAD COVER SUB-ASSEMBLY LH |
Temporarily install 2 service stud bolts (8 mm x 1.25 pitch with a length of 30 mm or more) to the 2 locations shown in the illustration.
![]() |
Apply seal packing as shown in the illustration.
- Seal packing:
- Toyota Genuine Seal Packing Black, Three Bond 1207B or equivalent
Text in Illustration Seal Packing - NOTICE:
- Remove any oil from the contact surface.
- Install the cylinder head cover within 3 minutes and tighten the bolts within 15 minutes after applying seal packing.
- Do not start the engine for at least 2 hours after the installation.
![]() |
Install a new cylinder head cover gasket LH and new No. 4 cylinder head cover gasket to the cylinder head cover LH.
- NOTICE:
- Remove any oil from the contact surface.
Using the service stud bolts as guides, place the cylinder head cover LH on the cylinder head.
Remove the 2 service stud bolts.
Temporarily install the cylinder head cover LH with the 18 bolts and 4 nozzle holder clamp seats. Tighten the 18 bolts and 4 nozzle holder clamp seats in the order shown in the illustration.
- Torque:
- 10 N*m{102 kgf*cm, 7 ft.*lbf}
Text in Illustration Bolt Nozzle Holder Clamp Seat - HINT:
- After tightening the bolts, check that the bolts at step 16 and 24 are tightened to the specified torque.
![]() |
44. INSTALL CYLINDER HEAD COVER SUB-ASSEMBLY RH |
Temporarily install 2 service stud bolts (8 mm x 1.25 pitch with a length of 30 mm or more) to the 2 locations shown in the illustration.
![]() |
Apply seal packing as shown in the illustration.
- Seal packing:
- Toyota Genuine Seal Packing Black, Three Bond 1207B or equivalent
Text in Illustration Seal Packing - NOTICE:
- Remove any oil from the contact surface.
- Install the cylinder head cover within 3 minutes and tighten the bolts within 15 minutes after applying seal packing.
- Do not start the engine for at least 2 hours after the installation.
![]() |
Install a new cylinder head cover gasket RH and new No. 3 cylinder head cover gasket to the cylinder head cover RH.
- NOTICE:
- Remove any oil from the contact surface.
Using the service stud bolts as guides, place the cylinder head cover RH on the cylinder head.
Remove the 2 service stud bolts.
Temporarily install the cylinder head cover RH with the 19 bolts and 4 nozzle holder clamp seats. Tighten the 19 bolts and 4 nozzle holder clamp seats in the order shown in the illustration.
- Torque:
- 10 N*m{102 kgf*cm, 7 ft.*lbf}
Text in Illustration Bolt Nozzle Holder Clamp Seat - HINT:
- After tightening the bolts, check that the bolts at step 16 and 25 are tightened to the specified torque.
![]() |
45. INSTALL FUEL INJECTOR LH |
- NOTICE:
- Be sure to install the injector, holder clamp and bolt to their original positions.
- Before installing the injector, check for carbon, foreign matter, etc. on the seal surfaces of the cylinder head and injector. If there is foreign matter, remove it before installing the injector.
Install 4 new injection nozzle seats to the cylinder head.
![]() |
Apply a light coat of clean engine oil to 4 new O-rings.
Text in Illustration *1 New O-Ring
![]() |
Install the O-rings to each injector as shown in the illustration.
Insert the 4 injectors into the cylinder head.
- NOTICE:
- Insert the injector until it touches the nozzle seat surface.
- After installing the injector to the cylinder head, the O-ring may prevent the injector from fully seating. If so, pull out the injector and reinstall it.
- Always return an injector to the same place it was removed from.
For an injector that has been replaced with a new injector, register the injector compensation code (Click here).
Temporarily install 4 new washers and the 4 nozzle holder clamps with the 4 clamp bolts.
Text in Illustration *1 New Washer - NOTICE:
- When temporarily installing the nozzle holder clamp bolt to the nozzle holder clamp, make sure that the bolt and clamp are not at an angle.
![]() |
Temporarily install the common rail LH with the 2 bolts.
![]() |
Temporarily install 4 new injection pipes to the common rail and injector.
![]() |
Temporarily install the No. 2 nozzle leakage pipe and 4 used gaskets with the 4 injector hollow screws and 2 bolts.
Text in Illustration Injector Hollow Screw Bolt
![]() |
Tighten the 4 holder clamp bolts.
- Torque:
- 25 N*m{255 kgf*cm, 18 ft.*lbf}
Remove the 4 injection pipes.
Remove the 2 bolts and common rail LH.
Remove the 4 injector hollow screws and 4 gaskets.
Remove the 2 bolts and No. 2 nozzle leakage pipe.
46. INSTALL FUEL INJECTOR RH |
- NOTICE:
- Be sure to install the injector, holder clamp and bolt to their original positions.
- Before installing the injector, check for carbon, foreign matter, etc. on the seal surfaces of the cylinder head and injector. If there is foreign matter, remove it before installing the injector.
Install 4 new injection nozzle seats to the cylinder head.
![]() |
Apply a light coat of clean engine oil to 4 new O-rings.
Text in Illustration *1 New O-Ring
![]() |
Install the O-rings to each injector as shown in the illustration.
Insert the 4 injectors into the cylinder head.
- NOTICE:
- Insert the injector until it touches the nozzle seat surface.
- After installing the injector to the cylinder head, the O-ring may prevent the injector from fully seating. If so, pull out the injector and reinstall it.
- Always return an injector to the same place it was removed from.
For an injector that has been replaced with a new injector, register the injector compensation code (Click here).
Temporarily install 4 new washers and the 4 nozzle holder clamps with the 4 clamp bolts.
Text in Illustration *1 New Washer - NOTICE:
- When temporarily installing the nozzle holder clamp bolt to the nozzle holder clamp, make sure that the bolt and clamp are not at an angle.
![]() |
Temporarily install the common rail RH with the 2 bolts.
![]() |
Temporarily install 4 new injection pipes to the common rail and injector.
![]() |
Temporarily install the No. 1 nozzle leakage pipe and 4 used gaskets with the 4 injector hollow screws and union bolt.
Text in Illustration Injector Hollow Screw Union Bolt
![]() |
Tighten the 4 holder clamp bolts.
- Torque:
- 25 N*m{255 kgf*cm, 18 ft.*lbf}
Remove the 4 injection pipes.
Remove the 2 bolts and common rail RH.
Remove the 4 injector hollow screws and 4 gaskets.
Remove the union bolt and No. 1 nozzle leakage pipe.
47. REMOVE INTAKE MANIFOLD |
Remove the 16 bolts, 2 gaskets and intake manifold.
Remove the 9 bolts, No. 1 intake manifold and gasket.
Remove the 9 bolts, No. 2 intake manifold and gasket.
48. INSTALL CYLINDER HEAD COVER INSULATOR LH |
49. INSTALL CYLINDER HEAD COVER INSULATOR RH |
50. INSTALL NO. 2 FUEL PUMP BRACKET |
Install the No. 2 fuel pump bracket with the bolt.
- Torque:
- 10 N*m{102 kgf*cm, 7 ft.*lbf}
51. INSTALL OIL SEPARATOR ASSEMBLY |
Install a new gasket to the oil separator.
- NOTICE:
- Remove any oil from the contact surface.
Install the oil separator with the 3 bolts.
- Torque:
- 10 N*m{102 kgf*cm, 7 ft.*lbf}
52. INSTALL VACUUM PUMP ASSEMBLY |
Apply engine oil to 2 new O-rings.
![]() |
Install the 2 O-rings to the vacuum pump.
Install the vacuum pump so that the coupling teeth of the vacuum pump (labeled A) and the groove of the camshaft (labeled B) are aligned.
- NOTICE:
- Be careful not to damage the O-ring.
![]() |
Install the vacuum pump with the 3 bolts.
- Torque:
- 21 N*m{214 kgf*cm, 15 ft.*lbf}
- NOTICE:
- Confirm that the vacuum pump is not at an angle, and that there is no clearance between the fitting surfaces.
![]() |
53. INSTALL GLOW PLUG ASSEMBLY |
Clean the glow plug and glow plug hole.
Apply adhesive to 3 or more thread roots in the area shown in the illustration.
- Adhesive:
- Toyota Genuine Adhesive 1324, Three Bond 1324 or equivalent
Text in Illustration *a 12 Thread Roots
![]() |
Using a 10 mm deep socket wrench, install the 8 glow plugs.
- Torque:
- 12 N*m{125 kgf*cm, 9 ft.*lbf}
54. INSTALL NO. 1 GLOW PLUG CONNECTOR |
Install the 2 glow plug connectors by uniformly tightening the 8 nuts.
- Torque:
- 2.2 N*m{22 kgf*cm, 19 in.*lbf}
Install the 8 screw grommets.
Connect the 2 wire harnesses with the 2 nuts and 2 screw grommets.
- Torque:
- 4.0 N*m{41 kgf*cm, 35 in.*lbf}
55. INSTALL WATER OUTLET PIPE |
Install 2 new gaskets and the water outlet pipe with the 4 bolts.
- Torque:
- 21 N*m{214 kgf*cm, 15 ft.*lbf}
- HINT:
- The gasket claw should face toward the water outlet pipe.
56. INSTALL WATER OUTLET |
Install a new gasket and the water outlet with the 2 bolts, and then connect the water outlet to the No. 2 water hose joint.
- Torque:
- 21 N*m{214 kgf*cm, 15 ft.*lbf}
57. INSTALL NO. 2 INTERCOOLER SUPPORT BRACKET |
Install the No. 2 intercooler support bracket with the 2 bolts.
- Torque:
- 43 N*m{438 kgf*cm, 32 ft.*lbf}
58. INSTALL STARTER HOSE BRACKET |
Install the starter hose bracket with the 2 bolts.
- Torque:
- 10 N*m{102 kgf*cm, 7 ft.*lbf}
59. INSTALL STARTER ASSEMBLY |
Install the starter with the 2 bolts.
- Torque:
- 80 N*m{816 kgf*cm, 59 ft.*lbf}
Connect the 2 starter hoses.
Text in Illustration *1 Yellow Mark
![]() |
Attach the harness clamp and connect the wire harness.
Connect the starter wire with the nut.
- Torque:
- 20 N*m{200 kgf*cm, 14 ft.*lbf}
Connect the starter connector.
60. INSTALL WATER PUMP ASSEMBLY |
Temporarily install a new gasket and the water pump with the 9 bolts and 2 nuts.
Bolt Length Item Length Bolt A 30 mm (1.18 in.) Bolt B 80 mm (3.15 in.)
![]() |
Uniformly tighten the 9 bolts and 2 nuts of the water pump in the order shown in the illustration.
- Torque:
- 25 N*m{250 kgf*cm, 18 ft.*lbf}
- NOTICE:
- After installing all of the bolts and nuts, check that all of the bolts and nuts are tightened to the torque specification.
![]() |
61. CONNECT INLET WATER HOSE |
62. INSTALL NO. 2 IDLER PULLEY BRACKET (w/ Viscous Heater) |
Temporarily install the No. 2 idler pulley bracket with the bolt.
![]() |
Temporarily install the 2 bolts to the No. 2 idler pulley bracket bolt hole.
Uniformly tighten the 3 bolts of the No. 2 idler pulley bracket in the order shown in the illustration.
- Torque:
- 49 N*m{495 kgf*cm, 36 ft.*lbf}
![]() |
63. INSTALL NO. 2 IDLER PULLEY (w/ Viscous Heater) |
Install the collar, No. 2 idler pulley and cover with the bolt.
- Torque:
- 49 N*m{495 kgf*cm, 36 ft.*lbf}
![]() |
64. INSTALL FAN BRACKET SUB-ASSEMBLY |
Install the fan bracket with the 4 bolts.
- Torque:
- 21 N*m{214 kgf*cm, 15 ft.*lbf}
Bolt Length Item Length Bolt A 30 mm (1.18 in.) Bolt B 80 mm (3.15 in.)
![]() |
65. INSTALL TIMING GEAR COVER INSULATOR |
w/o Viscous Heater:
Install the timing gear cover insulator with the 2 bolts.- Torque:
- 21 N*m{214 kgf*cm, 15 ft.*lbf}
w/ Viscous Heater:
Install the timing gear cover insulator.
66. INSTALL THERMOSTAT |
Install a new gasket to the thermostat.
- NOTICE:
- When installing the gasket to the thermostat, be careful not to deform the gasket. Make sure that the groove of the gasket is properly installed onto the thermostat, as shown in the illustration.
![]() |
Insert the thermostat into the water pump with the jiggle valve facing straight upward.
- HINT:
- The jiggle valve may be set within 30° of either side of the prescribed position.
67. INSTALL WATER INLET |
Install the water inlet with the 4 bolts.
- Torque:
- for bolt A:
- 21 N*m{214 kgf*cm, 15 ft.*lbf}
- for bolt B:
- 25 N*m{250 kgf*cm, 18 ft.*lbf}
![]() |
Connect the No. 2 oil cooler hose to the clamp and water pump.
![]() |
68. INSTALL NO. 1 IDLER PULLEY BRACKET (w/ Viscous Heater) |
Install the No. 1 idler pulley bracket with the bolt.
- Torque:
- 49 N*m{495 kgf*cm, 36 ft.*lbf}
![]() |
69. INSTALL VISCOUS HEATER ASSEMBLY WITH MAGNET CLUTCH (w/ Viscous Heater) |
![]() |
Install the heater assembly with the 2 bolts.
- Torque:
- 48.5 N*m{495 kgf*cm, 36 ft.*lbf}
Connect the 2 heater hoses.
Using pliers, grip the claws of the clips and slide the 2 clips.
Connect the connector and attach the clamp.
70. INSTALL CRANKSHAFT POSITION SENSOR |
![]() |
Apply a light coat of engine oil to the O-ring.
- NOTICE:
- When reusing the sensor, inspect the O-ring.
- If the O-ring has scratches or cuts, replace the sensor.
Install the sensor with the bolt.
- Torque:
- 5.0 N*m{51 kgf*cm, 44 in.*lbf}
![]() |
Connect the sensor wire harness clamp.
71. INSTALL CAMSHAFT POSITION SENSOR |
![]() |
Apply a light coat of engine oil to the O-ring.
- NOTICE:
- When reusing the sensor, inspect the O-ring.
- If the O-ring has scratches or cuts, replace the sensor.
Install the sensor with the bolt.
- Torque:
- 5.0 N*m{51 kgf*cm, 44 in.*lbf}
![]() |
Connect the sensor connector.
72. INSTALL NO. 1 OIL PAN SUB-ASSEMBLY |
- NOTICE:
- When the contact surfaces shown below are wet, wipe them with an oil-free cloth before applying seal packing.

Install the cylinder block oil hole gasket.
Apply a light coat of engine oil to 3 new O-rings and set the 3 O-rings to the oil regulator and scavenging pump.
Apply seal packing to the No. 1 oil pan as shown in the illustration.
- Standard seal diameter:
- 3.5 to 4.0 mm (0.134 to 0.157 in.)
- Seal packing:
- Toyota Genuine Seal Packing Black, Three Bond 1207B or equivalent
- NOTICE:
- For the 3 bolt holes labeled with arrows, apply the seal packing on the outer edges. For the other bolt holes, apply the seal packing on the inner edges.
- Make sure to apply a continuous bead of seal packing as shown in the illustration. If the bead breaks, overlap 3 mm (0.118 in.) of seal packing and continue the bead.
- Remove any oil and old seal packing from the contact surface.
- Install the No. 1 oil pan within 3 minutes and tighten the bolts and nuts within 15 minutes after applying seal packing.
- Do not start the engine for at least 2 hours after installing.
![]() |
Install the No. 1 oil pan and oil reflector plate with the 20 bolts and 2 nuts.
- Torque:
- 25 N*m{250 kgf*cm, 18 ft.*lbf}
Bolt Length Item Quantity Length Bolt A 7 70 mm (2.76 in.) Bolt B 8 20 mm (0.787 in.) Bolt C 5 30 mm (1.18 in.)
![]() |
73. INSTALL OIL STRAINER SUB-ASSEMBLY |
Apply a light coat of engine oil to a new O-ring, and install it to the oil strainer.
Install the oil strainer with the 2 bolts.
- Torque:
- 10 N*m{102 kgf*cm, 7 ft.*lbf}
74. INSTALL NO. 2 OIL PAN SUB-ASSEMBLY |
- NOTICE:
- When the contact surfaces shown below are wet, wipe them with an oil-free cloth before applying seal packing.
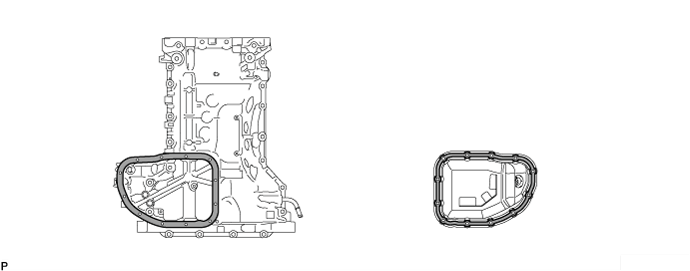
Apply seal packing to the No. 2 oil pan as shown in the illustration.
- Standard seal diameter:
- 5.0 to 6.0 mm (0.197 to 0.236 in.)
- Seal packing:
- Toyota Genuine Seal Packing Black, Three Bond 1207B or equivalent
- NOTICE:
- For the bolt and pin holes, make sure to apply seal packing to the inner sides.
- Make sure to apply a continuous bead of seal packing as shown in the illustration. If the bead breaks, overlap 3.0 mm (0.118 in.) of seal packing and continue the bead.
- Remove any oil from the contact surface.
- Install the No. 2 oil pan within 3 minutes and tighten the bolts and nuts within 10 minutes after applying seal packing.
- Do not start the engine for at least 2 hours after installing.
![]() |
Install the No. 2 oil pan with the 10 bolts and 2 nuts.
- Torque:
- 10 N*m{102 kgf*cm, 7 ft.*lbf}
75. INSTALL ENGINE OIL LEVEL SENSOR |
Install a new gasket to the sensor.
Install the sensor with the 4 bolts.
- Torque:
- 10 N*m{102 kgf*cm, 7 ft.*lbf}
![]() |
Connect the sensor connector.
76. INSTALL OIL FILTER BRACKET SUB-ASSEMBLY |
Apply a light coat of engine oil to 2 new O-rings, and set them to the oil filter bracket.
![]() |
Install the oil filter bracket with the 3 bolts and 2 nuts.
- Torque:
- 21 N*m{214 kgf*cm, 15 ft.*lbf}
Connect the 2 wire harness clamps.
77. INSTALL OIL FILTER ELEMENT |
Clean the inside of the oil filter cap, its threads and its O-ring groove.
![]() |
Apply a small amount of engine oil to a new O-ring and install it to the oil filter cap.
Set a new oil filter element in the oil filter cap.
Remove any dirt or foreign matter from the installation surface of the engine.
Apply a small amount of engine oil to the O-ring again and temporarily install the oil filter cap by hand.
Using SST, tighten the oil filter cap.
- SST
- 09228-06501
- Torque:
- 25 N*m{255 kgf*cm, 18 ft.*lbf}
- NOTICE:
- Make sure that the oil filter is installed securely as shown in the illustration.
- Be careful that the O-ring does not get caught between any surrounding parts.
![]() |
Install the No. 2 engine under cover seal to the No. 2 engine under cover with the 2 bolts.
- Torque:
- 10 N*m{102 kgf*cm, 7 ft.*lbf}
![]() |
78. INSTALL TIMING GEAR COVER SPACER |
Install the timing gear cover spacer with the 2 bolts.
- Torque:
- 21 N*m{214 kgf*cm, 15 ft.*lbf}
79. INSTALL CRANKSHAFT PULLEY |
- NOTICE:
- This procedure is intended for removal/installation of the crankshaft pulley only. Do not use this procedure for removal/installation of the flywheel or the drive plate and ring gear.
Align the crankshaft pulley and the crankshaft knock pin, and temporarily install the crankshaft pulley with the 3 bolts.
Text in Illustration *1 Service Hole *2 Protrusion
![]() |
Install the 2 bolts to the bolt holes of the crankshaft rear side.
Using a bar, turn the crankshaft until the crankshaft pulley service hole is a little to the right of bottom dead center.
Install a 14 mm x 1.5 pitch service bolt with a length of 70 mm or more to the crankshaft pulley service hole, and hold the crankshaft using the timing chain cover protrusion.
Uniformly tighten the 3 bolts in 2 passes in the order shown in the illustration.
- Torque:
- 115 N*m{1168 kgf*cm, 84 ft.*lbf}
![]() |
Remove the service bolt.
80. CONNECT NO. 2 OIL COOLER HOSE |
Align the white paint marks on the oil cooler hose and oil filter bracket and connect the hose. Then connect the other side to the water pump and attach the oil cooler hose to the clamp.
- NOTICE:
- Make sure to maintain a space between the oil cooler hose and crankshaft pulley, and the oil cooler hose and V-ribbed belt idler pulley.
81. CONNECT NO. 1 OIL COOLER HOSE |
Face the pink paint mark on the oil cooler hose toward the front side of the engine and connect the hose to the oil filter bracket. Then connect the other side to the water pump.
- NOTICE:
- Make sure to maintain a space between the oil cooler hose and crankshaft pulley.
82. INSTALL V-RIBBED BELT TENSIONER ASSEMBLY |
Install the V-ribbed belt tensioner with the 5 bolts.
- Torque:
- for bolt A and C:
- 43 N*m{438 kgf*cm, 32 ft.*lbf}
- for bolt B:
- 21 N*m{214 kgf*cm, 15 ft.*lbf}
Bolt Length Item Quantity Length Bolt A 1 116 mm (4.57 in.) Bolt B 2 40 mm (1.58 in.) Bolt C 2 95 mm (3.74 in.)
![]() |
Install the No. 1 idler pulley with the bolt.
- Torque:
- 43 N*m{438 kgf*cm, 32 ft.*lbf}
Install the V-ribbed belt tensioner bracket with the 3 bolts.
- Torque:
- 10 N*m{102 kgf*cm, 7 ft.*lbf}
83. INSTALL STIFFENER INSULATOR RH |
Install the stiffener insulator RH with the 2 bolts.
- Torque:
- 10 N*m{102 kgf*cm, 7 ft.*lbf}
84. INSTALL COMPRESSOR BRACKET |
Install the compressor bracket with the bolt.
- Torque:
- 21 N*m{214 kgf*cm, 15 ft.*lbf}
85. INSTALL NO. 2 CYLINDER BLOCK INSULATOR |
86. INSTALL ENGINE MOUNTING BRACKET LH |
Install the engine mounting bracket LH with the 4 bolts.
- Torque:
- 80 N*m{816 kgf*cm, 59 ft.*lbf}
87. INSTALL NO. 2 WATER BY-PASS PIPE SUB-ASSEMBLY |
Temporarily install a new gasket and No. 2 water by-pass pipe with the union bolt and 2 bolts.
![]() |
Tighten the union bolt and 2 bolts of the No. 2 water by-pass pipe in the order shown in the illustration.
- Torque:
- for union bolt:
- 35 N*m{357 kgf*cm, 26 ft.*lbf}
- for bolt:
- 10 N*m{102 kgf*cm, 7 ft.*lbf}
88. INSTALL NO. 3 VACUUM TRANSMITTING PIPE SUB-ASSEMBLY |
Install the No. 3 vacuum transmitting pipe with the 2 bolts.
- Torque:
- 6.0 N*m{61 kgf*cm, 53 in.*lbf}
w/ Intercooler:
Connect the vacuum hose.
89. INSTALL TURBOCHARGER WIRE |
Install the turbocharger wire with the 2 bolts.
- Torque:
- 21 N*m{214 kgf*cm, 15 ft.*lbf}
Attach the 3 wire harness clamps.
90. INSTALL NO. 2 INTAKE AIR CONNECTOR BRACKET |
Install the No. 2 intake air connector bracket with the bolt.
- Torque:
- 21 N*m{214 kgf*cm, 15 ft.*lbf}
Attach the 2 wire clamps.
91. INSTALL NO. 1 CYLINDER BLOCK INSULATOR |
92. INSTALL ENGINE MOUNTING BRACKET RH |
Install the engine mounting bracket RH with the 4 bolts.
- Torque:
- 80 N*m{816 kgf*cm, 59 ft.*lbf}
93. INSTALL NO. 4 VACUUM TRANSMITTING PIPE SUB-ASSEMBLY |
Install the No. 4 vacuum transmitting pipe with the 2 bolts.
- Torque:
- 6.0 N*m{61 kgf*cm, 53 in.*lbf}
Connect the vacuum hose.
94. INSTALL NO. 1 WATER BY-PASS PIPE SUB-ASSEMBLY |
Temporarily install a new gasket and the No. 1 water by-pass pipe with the union bolt and bolt.
Tighten the union bolt and bolt of the No. 1 water by-pass pipe in the order shown in the illustration.
- Torque:
- for union bolt:
- 35 N*m{357 kgf*cm, 26 ft.*lbf}
- for bolt:
- 10 N*m{102 kgf*cm, 7 ft.*lbf}
![]() |
95. INSTALL AIR TUBE SUPPORT |
Install the air tube support with the 2 bolts.
- Torque:
- 21 N*m{214 kgf*cm, 15 ft.*lbf}
96. INSTALL NO. 1 INTAKE AIR CONNECTOR BRACKET |
Install the No. 1 intake air connector bracket with the 2 bolts.
- Torque:
- 21 N*m{214 kgf*cm, 15 ft.*lbf}
97. INSTALL GENERATOR ASSEMBLY |
Temporarily install the generator with the 3 bolts and 2 nuts.
![]() |
Uniformly tighten the 3 bolts and 2 nuts in the order shown in the illustration.
- Torque:
- 21 N*m{214 kgf*cm, 15 ft.*lbf}
Connect the generator cable and install the nut and bolt.
- Torque:
- for bolt:
- 13 N*m{133 kgf*cm, 10 ft.*lbf}
- for nut (130A Type and 150A Type:):
- 9.8 N*m{100 kgf*cm, 87 in.*lbf}
- for nut (180A Type:):
- 12 N*m{122 kgf*cm, 9 ft.*lbf}
98. INSTALL NO. 1 TURBOCHARGER SUB-ASSEMBLY WITH EXHAUST MANIFOLD RH AND NO. 2 TURBOCHARGER SUB-ASSEMBLY WITH EXHAUST MANIFOLD LH |
99. CONNECT CABLE TO NEGATIVE BATTERY TERMINAL |
- NOTICE:
- When disconnecting the cable, some systems need to be initialized after the cable is reconnected (Click here).
Connect the cables to the negative (-) main battery and sub-battery terminals.