CHECK PARK/NEUTRAL POSITION SWITCH ASSEMBLY (POWER SOURCE)
CHECK HARNESS AND CONNECTOR (ECM OUTPUT SIGNAL)
INSPECT PARK/NEUTRAL POSITION SWITCH ASSEMBLY
CHECK TRANSMISSION CONTROL SWITCH (POWER SOURCE)
INSPECT TRANSMISSION CONTROL SWITCH
CHECK HARNESS AND CONNECTOR (BATTERY - ECM)
CHECK HARNESS AND CONNECTOR (PARK/NEUTRAL POSITION SWITCH - ECM)
DTC P0705 Transmission Range Sensor Circuit Malfunction (PRNDL Input) |
DESCRIPTION
The Park/Neutral Position (PNP) switch detects the shift lever position and sends signals to the ECM.DTC Code | DTC Detection Condition
| Trouble Area |
P0705 |
|
|
MONITOR DESCRIPTION
This DTC indicates a problem with the park/neutral position switch or the wire harness in the park/neutral position switch circuit.The park/neutral position switch detects the shift lever position and sends a signal to the ECM.
For security, the park/neutral position switch detects the shift lever position so that the engine can be started only when the shift lever is in P or N.
The park/neutral position switch sends a signal to the ECM according to the shift lever position (P, R, N, D or M).
The ECM determines that there is a problem with the switch or related parts if it receives more than 1 position signal simultaneously. The ECM will illuminate the MIL and store the DTC.
WIRING DIAGRAM
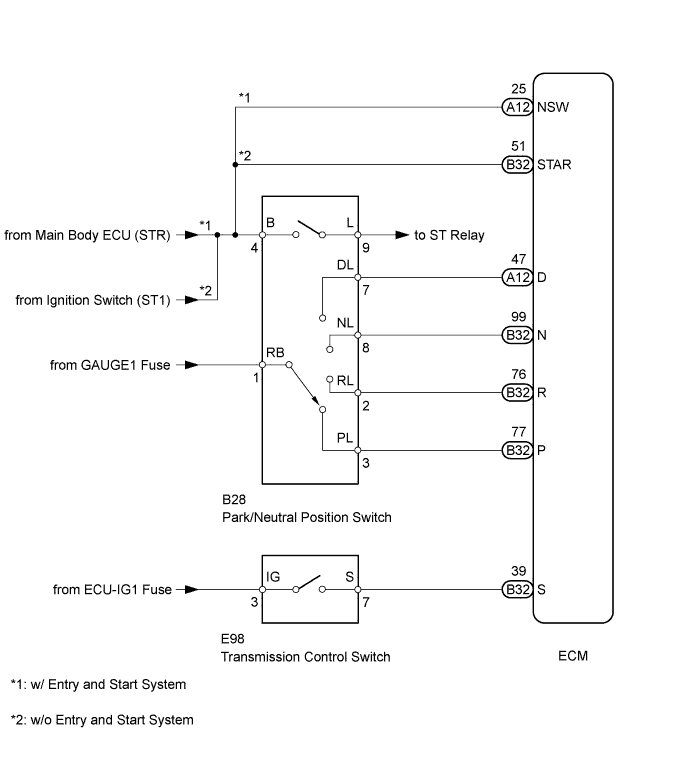
INSPECTION PROCEDURE
- *1: w/ VSC
- *2: w/o VSC
DATA LIST |
- HINT:
- Using the intelligent tester to read the Data List allows the values or states of switches, sensors, actuators and other items to be read without removing any parts. This non-intrusive inspection can be very useful because intermittent conditions or signals may be discovered before parts or wiring is disturbed. Reading the Data List information early in troubleshooting is one way to save diagnostic time.
- NOTICE:
- In the table below, the values listed under "Normal Condition" are reference values. Do not depend solely on these reference values when deciding whether a part is faulty or not.
Warm up the engine.
Turn the ignition switch off.
Connect the intelligent tester to the DLC3.
Turn the ignition switch to ON.
Turn the intelligent tester on.
Enter the following menus: Powertrain / Engine and ECT / Data List.
According to the display on the tester, read the Data List.
Engine and ECT Tester Display Measurement Item/Range Normal Condition Diagnostic Note Neutral Position SW Signal PNP switch status/
ON or OFF- ON: Shift lever in P or N
- OFF: Shift lever not in P or N
When the shift lever position displayed on the intelligent tester differs from the actual position, the adjustment of the PNP switch or shift cable may be incorrect. Shift SW Status (P Range) PNP switch status/
ON or OFF- ON: Shift lever in P
- OFF: Shift lever not in P
Shift SW Status (R Range) PNP switch status/
ON or OFF- ON: Shift lever in R
- OFF: Shift lever not in R
Shift SW Status (N Range) PNP switch status/
ON or OFF- ON: Shift lever in N
- OFF: Shift lever not in N
Sports Shift Up SW Sport shift up switch status/
ON or OFF- ON: Shift lever held in "+" (up-shift)
- OFF: Shift lever not held in "+" (up-shift)
- - ON: "+" shift paddle operated and held (up-shift)
- OFF: "+" shift paddle not operated (up-shift)
Sports Shift Down SW Sport shift down switch status/
ON or OFF- ON: Shift lever held in "-" (down-shift)
- OFF: Shift lever not held in "-" (down-shift)
- - ON: "-" shift paddle operated and held (down-shift)
- OFF: "-" shift paddle not operated (down-shift)
Sports Mode Selection SW Sport mode select switch status/
ON or OFF- ON: Shift lever in M, "+" or "-"
- OFF: Shift lever not in M, "+" or "-"
- Shift SW Status (D Range) PNP switch status/
ON or OFF- ON: Shift lever in D
- OFF: Shift lever not in D
When the shift lever position displayed on the intelligent tester differs from the actual position, the adjustment of the PNP switch or shift cable may be incorrect. - ON: Shift lever in P or N
1.CHECK PARK/NEUTRAL POSITION SWITCH ASSEMBLY (POWER SOURCE) |
Disconnect the park/neutral position switch connector.
![]() |
Measure the voltage according to the value(s) in the table below.
- Standard Voltage:
Tester Connection Switch Condition Specified Condition B28-1 (RB) - Body ground Ignition switch ON 11 to 14 V B28-1 (RB) - Body ground Ignition switch off Below 1 V
Text in Illustration *1 Front view of wire harness connector
(to Park/Neutral Position Switch)
|
| ||||
OK | |
2.CHECK HARNESS AND CONNECTOR (ECM OUTPUT SIGNAL) |
Disconnect the park/neutral position switch connector.
![]() |
Measure the voltage according to the value(s) in the table below.
- Standard Voltage:
Tester Connection Switch Condition Specified Condition B28-4 (B) - Body ground Ignition switch ON 11 to 14 V B28-4 (B) - Body ground Ignition switch off Below 1 V
Text in Illustration *1 Front view of wire harness connector
(to Park/Neutral Position Switch)
|
| ||||
OK | |
3.INSPECT PARK/NEUTRAL POSITION SWITCH ASSEMBLY |
Disconnect the park/neutral position switch connector.
![]() |
Measure the resistance according to the value(s) in the table below.
- Standard Resistance:
Tester Connection Condition Specified Condition - 1 (RB) - 3 (PL)
- 4 (B) - 9 (L)
Shift lever in P Below 1 Ω 1 (RB) - 2 (RL) Shift lever in R Below 1 Ω - 1 (RB) - 8 (NL)
- 4 (B) - 9 (L)
Shift lever in N Below 1 Ω 1 (RB) - 7 (DL) Shift lever in D, M, "+" or "-" Below 1 Ω - 1 (RB) - 3 (PL)
- 4 (B) - 9 (L)
Shift lever not in P 10 kΩ or higher 1 (RB) - 2 (RL) Shift lever not in R 10 kΩ or higher - 1 (RB) - 8 (NL)
- 4 (B) - 9 (L)
Shift lever not in N 10 kΩ or higher 1 (RB) - 7 (DL) Shift lever not in D, M, "+" or "-" 10 kΩ or higher - 1 (RB) - 3 (PL)
Text in Illustration *1 Component without harness connected
(Park/Neutral Position Switch)
|
| ||||
OK | |
4.CHECK TRANSMISSION CONTROL SWITCH (POWER SOURCE) |
Disconnect the transmission control switch connector.
![]() |
Measure the voltage according to the value(s) in the table below.
- Standard Voltage:
Tester Connection Switch Condition Specified Condition E98-3 (IG) - Body ground Ignition switch ON 11 to 14 V E98-3 (IG) - Body ground Ignition switch off Below 1 V
Text in Illustration *1 Front view of wire harness connector
(to Transmission Control Switch)
|
| ||||
OK | |
5.INSPECT TRANSMISSION CONTROL SWITCH |
Disconnect the transmission control switch connector.
![]() |
Measure the resistance according to the value(s) in the table below.
- Standard Resistance:
Tester Connection Condition Specified Condition 3 (IG) - 7 (S) Shift lever in M, "+" or "-" Below 1 Ω 3 (IG) - 7 (S) Shift lever not in M, "+" or "-" 10 kΩ or higher
Text in Illustration *1 Component without harness connected
(Transmission Control Switch)
|
| ||||
OK | |
6.CHECK HARNESS AND CONNECTOR (BATTERY - ECM) |
Disconnect the ECM connectors.
![]() |
Measure the voltage according to the value(s) in the table below.
- Standard Voltage:
Tester Connection Condition Specified Condition B32-77 (P) - Body ground - Ignition switch ON
- Shift lever in P
11 to 14 V B32-76 (R) - Body ground - Ignition switch ON
- Shift lever in R
11 to 14 V* B32-99 (N) - Body ground - Ignition switch ON
- Shift lever in N
11 to 14 V A12-47 (D) - Body ground - Ignition switch ON
- Shift lever in D
11 to 14 V B32-39 (S) - Body ground - Ignition switch ON
- Shift lever in M, "+" or "-"
11 to 14 V B32-77 (P) - Body ground - Ignition switch ON
- Shift lever not in P
Below 1 V B32-76 (R) - Body ground - Ignition switch ON
- Shift lever not in R
Below 1 V B32-99 (N) - Body ground - Ignition switch ON
- Shift lever not in N
Below 1 V A12-47 (D) - Body ground - Ignition switch ON
- Shift lever not in D
Below 1 V B32-39 (S) - Body ground - Ignition switch ON
- Shift lever not in M, "+" or "-"
Below 1 V - Ignition switch ON
Text in Illustration *1 Front view of wire harness connector
(to ECM)- HINT:
- *: The voltage will drop slightly due to the illumination of the back-up light.
|
| ||||
OK | |
7.REPLACE ECM |
Replace the ECM (RAV4_ACA30 RM0000017UO01KX.html).
NEXT | |
8.PERFORM INITIALIZATION |
- NOTICE:
- Performing reset memory will clear the learned values of both the yaw rate sensor assembly*1 or deceleration sensor*2 (deceleration sensor 0 point calibration) and CVT oil pressure (CVT oil pressure calibration). Make sure to perform reset memory, yaw rate sensor assembly*1 or deceleration sensor*2 0 point calibration and CVT oil pressure calibration when replacing any of the parts shown in the following table:
Replaced Part - Continuously variable transaxle assembly
- ECM
- Oil pressure sensor
- Yaw rate sensor assembly (w/ VSC)
- Deceleration sensor (w/o VSC)
- Brake actuator assembly (skid control ECU)
- Continuously variable transaxle assembly
- After performing reset memory, always perform yaw rate sensor assembly*1 or deceleration sensor*2 (deceleration sensor 0 point) calibration first, and then CVT oil pressure calibration.
- Always perform 0 point calibration with the vehicle on level ground.
- Do not shake or vibrate the vehicle during 0 point calibration.
Using the intelligent tester, perform reset memory, deceleration sensor 0 point calibration and CVT oil pressure calibration (RAV4_ACA30 RM000003UQR002X.html).
Check that no DTC is stored.
NEXT | ||
|
9.CHECK HARNESS AND CONNECTOR (PARK/NEUTRAL POSITION SWITCH - ECM) |
Disconnect the park/neutral position switch connector.
![]() |
Disconnect the ECM connector.
Measure the resistance according to the value(s) in the table below.
- Standard Resistance:
w/ Entry and Start System Tester Connection Condition Specified Condition B28-4 (B) - A12-25 (NSW) Always Below 1 Ω B28-4 (B) - Body ground Always 10 kΩ or higher A12-25 (NSW) - Body ground Always 10 kΩ or higher w/o Entry and Start System Tester Connection Condition Specified Condition B28-4 (B) - B32-51 (STAR) Always Below 1 Ω B28-4 (B) - Body ground Always 10 kΩ or higher B32-51 (STAR) - Body ground Always 10 kΩ or higher
Text in Illustration *1 Front view of wire harness connector
(to Park/Neutral Position Switch)*2 Front view of wire harness connector
(to ECM)*3 w/ Entry and Start System *4 Front view of wire harness connector
(to ECM)*5 w/o Entry and Start System
|
| ||||
OK | |
10.REPLACE ECM |
Replace the ECM (RAV4_ACA30 RM0000017UO01KX.html).
NEXT | |
11.PERFORM INITIALIZATION |
- NOTICE:
- Performing reset memory will clear the learned values of both the yaw rate sensor assembly*1 or deceleration sensor*2 (deceleration sensor 0 point calibration) and CVT oil pressure (CVT oil pressure calibration). Make sure to perform reset memory, yaw rate sensor assembly*1 or deceleration sensor*2 0 point calibration and CVT oil pressure calibration when replacing any of the parts shown in the following table:
Replaced Part - Continuously variable transaxle assembly
- ECM
- Oil pressure sensor
- Yaw rate sensor assembly (w/ VSC)
- Deceleration sensor (w/o VSC)
- Brake actuator assembly (skid control ECU)
- Continuously variable transaxle assembly
- After performing reset memory, always perform yaw rate sensor assembly*1 or deceleration sensor*2 (deceleration sensor 0 point) calibration first, and then CVT oil pressure calibration.
- Always perform 0 point calibration with the vehicle on level ground.
- Do not shake or vibrate the vehicle during 0 point calibration.
Using the intelligent tester, perform reset memory, deceleration sensor 0 point calibration and CVT oil pressure calibration (RAV4_ACA30 RM000003UQR002X.html).
Check that no DTC is stored.
NEXT | ||
|