Compressor (For 1Kd-Ftv, 2Kd-Ftv) -- Installation |
1. ADJUST COMPRESSOR OIL |
When replacing the compressor and magnet clutch with a new one, gradually discharge the refrigerant gas from the service valve, and drain the following amount of oil from the new compressor and magnet clutch before installation.
- Standard:
- (Oil capacity inside the new compressor and magnet clutch: 80 + 15 cc (2.71 + 0.51 fl.oz)) - (Remaining oil amount in the removed compressor and magnet clutch) = (Oil amount to be removed from the new compressor)
- NOTICE:
- When checking the compressor oil level, follow the A/C system precautions.
- If a new compressor and magnet clutch is installed without removing the oil remaining in the pipes of the vehicle, the oil amount will be too large. This prevents heat exchange in the refrigerant cycle and causes refrigerant failure.
- If the volume of oil remaining in the removed compressor and magnet clutch is small, check for oil leakage.
- Be sure to use ND-OIL 8 or equivalent compressor oil.
2. INSTALL COOLER COMPRESSOR ASSEMBLY |
![]() |
Install the cooler compressor assembly with the 4 bolts and tighten the bolts in the order shown in the illustration.
- Torque:
- 25 N*m{250 kgf*cm, 18 ft.*lbf}
Connect the connector.
3. INSTALL NO. 1 COOLER REFRIGERANT DISCHARGE HOSE |
Remove the vinyl tape attached to the No. 1 cooler refrigerant discharge hose.
Sufficiently apply compressor oil to a new O-ring and the fitting surface of the compressor.
- Compressor oil:
- ND-OIL 8 or equivalent
Install the O-ring to the No. 1 cooler refrigerant discharge hose.
Connect the No. 1 cooler refrigerant discharge hose with the bolt.
- Torque:
- 9.8 N*m{100 kgf*cm, 87 in.*lbf}
4. INSTALL SUCTION HOSE SUB-ASSEMBLY |
Remove the vinyl tape attached to the suction hose sub-assembly.
Sufficiently apply compressor oil to a new O-ring and the fitting surface of the compressor.
- Compressor oil:
- ND-OIL 8 or equivalent
Install the O-ring to the suction hose sub-assembly.
Connect the suction hose sub-assembly with the bolt.
- Torque:
- 9.8 N*m{100 kgf*cm, 87 in.*lbf}
5. INSTALL FAN AND GENERATOR V BELT |
Rotate the V-ribbed belt tensioner pulley clockwise, and then install the fan and generator V belt.
- NOTICE:
- Make sure that the fan and generator V belt is set properly on each pulley.
Check that the indicator mark of the V-ribbed belt tensioner (HILUX_TGN26 RM000001475016X.html).
6. INSTALL AIR CLEANER ASSEMBLY |
Connect the air cleaner hose.
Install the cleaner with the 2 bolts.
- Torque:
- 14 N*m{143 kgf*cm, 10 ft.*lbf}
Tighten the hose clamp.
Connect the connector to the mass air flow meter connector.
7. CHARGE REFRIGERANT |
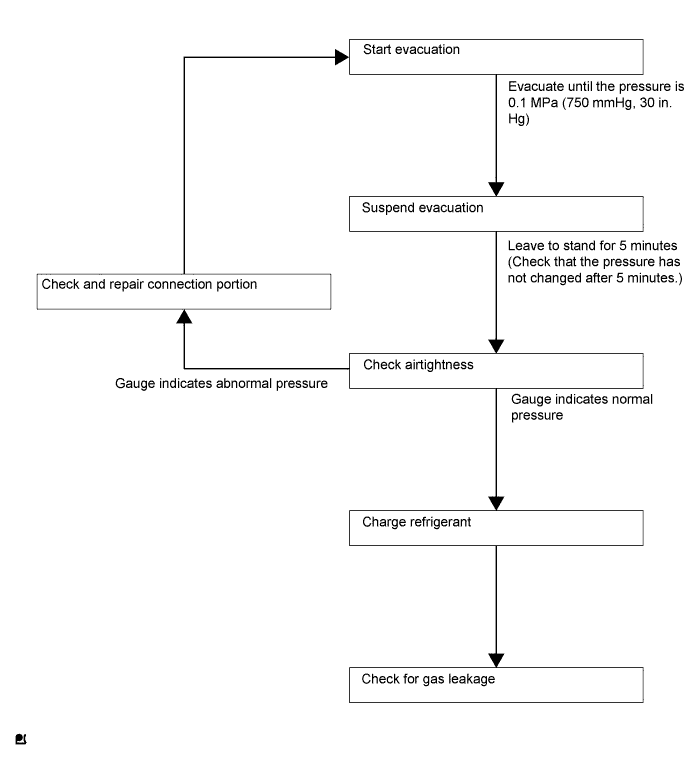
- HINT:
- Charge refrigerant in accordance with the equipment manual.
Perform vacuum purging using a vacuum pump.
Charge refrigerant HFC-134a (R134a).
- SST
- 09985-20010(09985-02130,09985-02150,09985-02090,09985-02110,09985-02010,09985-02050,09985-02060,09985-02070)
- Standard:
- 450 +/-30 g (15.9 +/-1.1 oz)
Text in Illustration *a Amount to be charged *b Charge 100 g (3.53 oz) *c Mean value in proper range *d Point where bubbles disappear *e Overcharged *f Pressure *g Sub-cool system *h Refrigerant amount - NOTICE:
- Do not operate the cooler compressor before charging refrigerant as the cooler compressor will not work properly without any refrigerant, and will overheat.
- The system may need to be charged with approximately 100 g (3.53 oz) of refrigerant after bubbles disappear. The refrigerant amount should be checked by measuring its quantity, and not with the sight glass.
8. WARM UP ENGINE |
Warm up the engine at less than 1850 rpm for 2 minutes or more after charging the refrigerant.
- NOTICE:
- Be sure to warm up the compressor by turning the A/C switch on after removing and installing the cooler refrigerant lines (including the compressor) to prevent damage to the compressor.
9. CHECK FOR LEAKAGE OF REFRIGERANT |
After recharging the refrigerant, check for refrigerant gas leakage using a halogen leak detector.
Perform the operation observing the following instructions:
- Stop the engine.
- Secure good ventilation (the halogen leak detector may react to volatile gases other than refrigerant, such as evaporated gasoline or exhaust gas).
- Repeat the test 2 or 3 times.
- Make sure that some refrigerant remains in the refrigeration system.
- HINT:
- When the compressor is off: approximately 392 to 588 kPa (4.0 to 6.0 kgf/cm2, 57 to 85 psi).
- Stop the engine.
Using a halogen leak detector, check the refrigerant line for leakage.
If a gas leak is not detected from the drain hose, remove the blower motor control (blower resistor) from the cooling unit. Insert the halogen leak detector sensor into the unit and check for gas leakage.
Disconnect the pressure switch connector and wait for approximately 20 minutes. Bring the halogen leak detector close to the pressure switch and check for gas leakage.
Text in Illustration *1 Halogen Leak Detector *a Check for Leakage